- Last-Mile
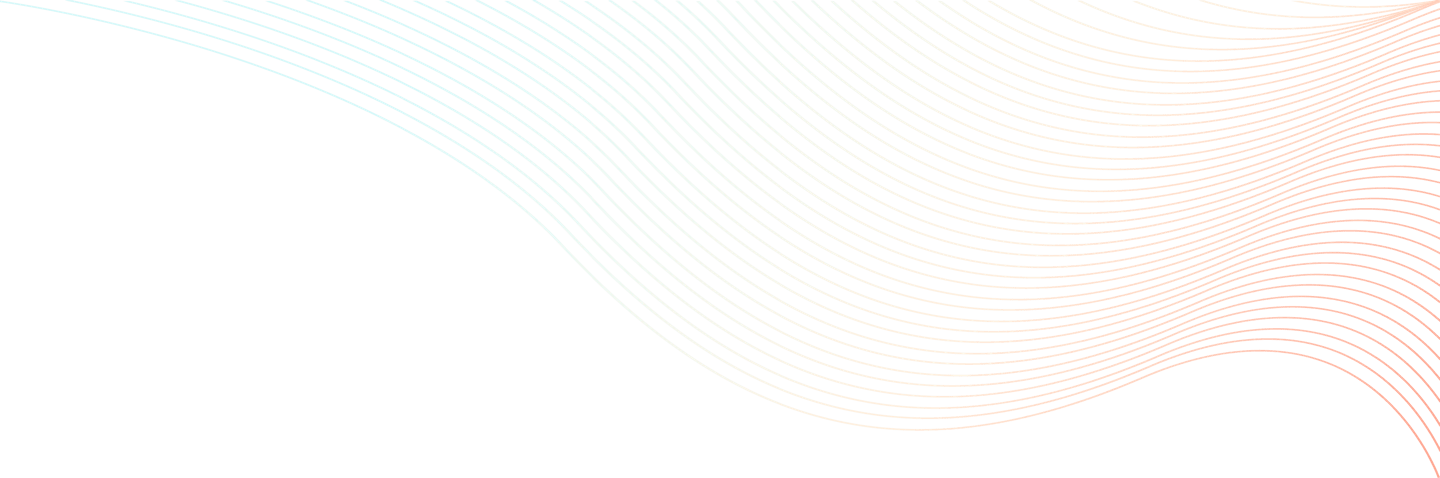
Last-mile optimization. Why is it important to modern day delivery operations?
Online retailers need to work hard to please e-commerce customers in this advanced digital age. Customers expect their products to be delivered accurately and quickly, at a low price, and in perfect condition. The highest standard of service needs to be consistently applied to maintain customer trust. To retain customers effectively, a top-notch logistics process including last mile delivery optimization must be in place that efficiently manages every aspect of the supply chain. A retailer’s survival depends on how efficiently they can manage their relationships with business partners.
Choosing Last-mile Optimization Software
The key to meeting customer demands lies in utilizing last-mile optimization software for tracking orders in real-time. While some businesses may choose to hire software professionals in-house to create custom applications, it is more often the best cost-saving to outsource services to an offshore vendor who can assist your company in transitioning to app development.
Mobile-based logistics applications increase overall functionality to integrate various aspects of the main system. They assist in increasing overall visibility by generating in-depth reports that summarize distribution processes. These reports may be used by the carriers in the last mile to develop a logistics process that goes step-by-step to maximize last-mile delivery performance.
Plans of action aided by the use of last-mile delivery optimization software help to delegate assets, between factory and warehouse operations and manpower. After last-mile software implementation is completed, a base set of last mile analytics data is generated by using historical data. This is an extremely valuable tool that can be analyzed to make better decisions, enhance procedures, and apply them correctly. This is crucial for carrying forth your company’s last-mile delivery solutions that are aimed at cutting costs and increasing positive outcomes for customers.
Optimize Operating Procedures in Logistics
Once you have established a realistic, measurable performance plan based on your established data set, plans may be set to establish a set of standard operating procedures. This may involve monitoring a driver’s performance. When routes are not integrated or poorly planned, it can result in a great loss of productivity, leaking out your enterprise’s resources. The driver’s time away from the distribution center should ideally be spent in driving along the most efficient route and unloading product, not waiting around or wasting time. With the help of last-mile optimization software, timelines are also monitored for loading time and vehicle checks.
The last-mile optimization software is also applied effectively to minimize errors in delivery and customer dissatisfaction. When customers complain about issues, specific data can be retrieved, and the issue's source may be easily assessed. These are also useful for predicting and avoiding future negative outcomes.
Tracking inventory needs to be extended through the entire logistics process, not only until the point of loading it on the truck. Last-minute delivery must also remain visible. This requires the proper application of last-mile optimization software to extend visibility throughout the entire logistics process.
Applying Last-mile Optimization to Manage Third-Party Drivers
The rapidly evolving e-commerce industry has created an on-demand boom. It has become common for businesses to use freelance drivers and local fleets that require tech apps to manage fleets locally. Technology vendors can also be hired to build a mobile app to manage drivers through a dashboard that integrates all the drivers into one system overview.
Route optimization requires data to help optimize routes in real-time. Tracking data is used to see what was delivered and what is to be delivered and how long it takes the driver to reach certain locations. This allows a company to plan the best routes.
As order volumes can be seen as more on some days and less on others, exact dates of anticipated high volumes can be assessed. More staff can be scheduled on those days, and less on others.
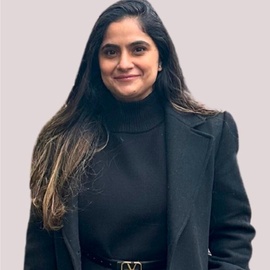
Komal Puri is a seasoned professional in the logistics and supply chain industry. As the AVP of Marketing and a subject matter expert at FarEye, she has been instrumental in shaping the industry narrative for the past decade. Her expertise and insights have earned her numerous awards and recognition. Komal’s writings reflect her deep understanding of the industry, offering valuable insights and thought leadership.
Let's Talk to Our Experts and Optimize Your Deliveries Today!
An expert from our team will reach out within 24 hours