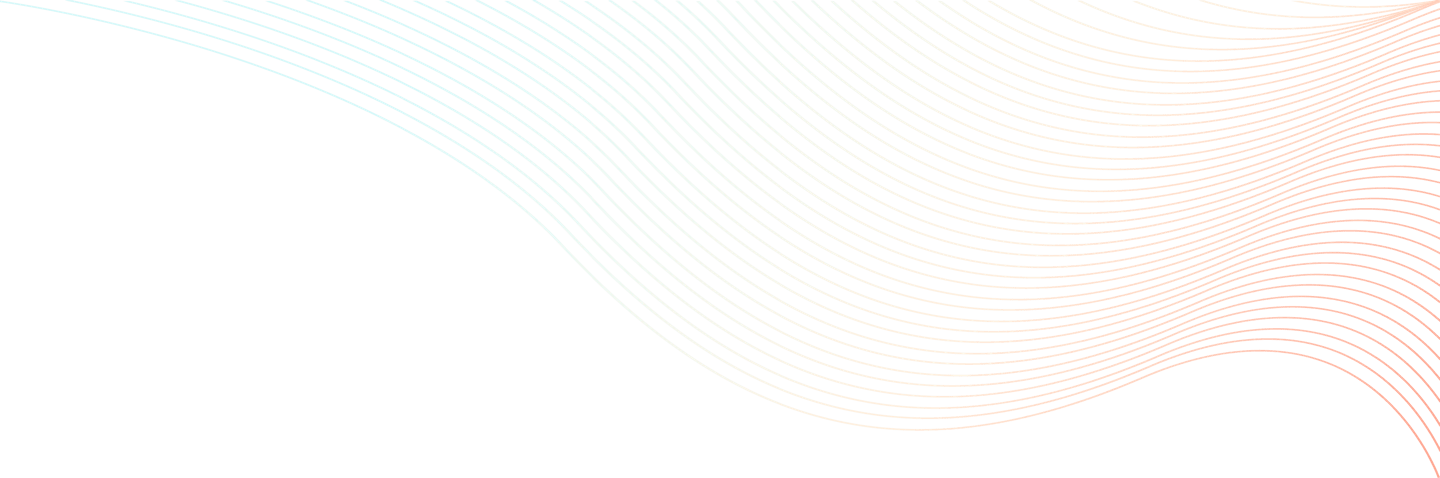
What is Cross-Docking? Cross-Docking vs Traditional Warehousing
Discover the differences between cross-docking and traditional warehousing, their advantages, and which option can optimize your supply chain efficiency and lower operational costs.
By Komal Puri | October 10, 2022
In today’s fast-paced world, speed and efficiency are crucial. However, businesses face several supply chain challenges. Such as rising transportation costs and customer demands.
To optimize operations, businesses use two key strategies: cross-docking and traditional warehousing.
Traditional warehousing offers long-term storage. It offers stability. This method works well for businesses like furniture retailers. As they need to stockpile inventory.
Cross-docking takes a different approach. It minimizes handling time. It also accelerates delivery. This method is ideal for perishable goods distributors. They require rapid turnover.
Choosing the right strategy is important. It would affect both operational efficiency and customer satisfaction.
In this blog, we will explore both the strategies. We guide you to choose best approach for your business.
What is cross-docking?
It includes directly transferring goods from inbound to outbound transport. It minimizes the need for storage. In a dedicated docking terminal, products are received, sorted and loaded onto outbound vehicles. Typically done within 24 hours. Cross-docking enhances operational efficiency. It also reduces handling costs.
Key industries using cross-docking include perishable goods like food, where speed preserves freshness. FMCG benefits from quick turnover and minimal storage time. Retailers, e-commerce companies and manufacturers use cross-docking to optimize inventory and speed up deliveries.
What is Traditional Warehousing?
It is a conventional method. Goods are stored in dedicated facilities for long periods. It helps businesses manage their inventory efficiently. The inventory is organized systematically and stored until needed. The primary focus is fulfilling customer orders gradually.
This approach helps industries like e-commerce. For them maintaining stock levels is crucial. Also seasonal inventory needs storage during off-peak times. Traditional warehousing ensures supply during demand spikes. They offer businesses stability and control. Traditional warehouses can accommodate large product volumes. They ensure safety and accessibility. Enabling seamless order processing.
Key Differences Between Cross-Docking and Traditional Warehousing
Below are the key differences based on various operational factors:
1. Storage Requirements
- Cross-Docking: Temporary Storage
Products move directly from inbound to outbound transport. Storage time is minimal or none. This method works best for perishable goods. Also for high-demand items. - Traditional Warehousing: Long-Term Storage
Goods are stored for long periods. This allows inventory to accumulate. It suits products with fluctuating demand. It also works for those needing longer lead times.
2. Operational Costs
- Cross-Docking: Lower Operational Costs
It reduces storage time and inventory costs. This lowers overall operational expenses. May require investment in specialized infrastructure and technology. - Traditional Warehousing: Higher Operational Costs: It offers flexibility in inventory management. It has higher costs. Such as expenses for storage space, labor and inventory management systems.
3. Turnaround Time
- Cross-Docking: Faster Turnaround Time: The process is built for speed. Goods move quickly from receiving to shipping docks. This reduces lead times. Customer orders are fulfilled faster.
- Traditional Warehousing: Longer Lead Times: Picking, packing and shipping take time. This can lead to longer turnaround times. It may not meet demands of just-in-time delivery models.
4. Flexibility
- Cross-Docking: Limited Flexibility: Works well for high-volume, fast-moving goods. It relies on immediate transfer. Less suitable for diverse products or fluctuating order sizes.
- Traditional Warehousing: Greater Flexibility: Businesses can store various products in different volumes. This flexibility helps with irregular demand. Also with large product catalogs.
Advantages of Cross-Docking vs Traditional Warehousing
These are 2 distinct approaches to inventory management. Here are the key advantages of both:
Advantages | Cross-Docking | Traditional Warehousing |
Storage Costs | Minimizes the need for storage, reducing costs significantly | Higher costs due to long-term inventory storage |
Delivery Speed | Facilitates faster delivery with minimal handling time | Slower delivery due to longer storage times |
Risk of Damage | Reduces the risk of product damage through less handling | Increased risk due to more handling and storage stages |
Operational Efficiency | Streamlined operations with fewer processes involved | More complex operations with multiple handling steps |
Inventory Management | Real-time inventory management, reducing excess stock | Relies on forecasting, leading to potential overstocking |
Flexibility | Less flexible, ideal for high-turnover goods | Offers flexibility for diverse inventory types and seasonal stockpiling |
Labor Costs | Reduces labor costs by minimizing handling and storage tasks | Higher labor costs associated with managing large inventories |
Environmental Impact | Lower emissions due to reduced transportation and storage needs | Higher emissions from larger facilities and longer transport times |
Challenges of Cross-Docking vs Traditional Warehousing
Both approaches have unique challenges, such as:
Challenges | Cross-Docking | Traditional Warehousing |
Product Suitability | It works only for items with quick turnover. Not ideal for fragile or climate-sensitive goods | Suitable for various products. Also supports those requiring long-term storage |
Coordination Requirements | High complexity due to reliance on precise timing and coordination among various stakeholders | Lower complexity; involves multiple teams but allows for more flexible planning |
Infrastructure Investment | Requires specialized facilities designed for rapid product flow, which can involve significant upfront costs | Typically requires less specialized infrastructure but may incur higher ongoing operational costs |
Risk Management | Increased risk of disruptions due to low inventory and reliance on transportation | More stable because of buffer stock, but risks include overstocking and inventory obsolescence |
Flexibility | Less flexible in responding to demand fluctuations due to low inventory levels | More adaptable to varying demand patterns, allowing for better inventory management |
Cost Implications | Lower storage costs but higher transportation expenses can deplete the savings | Long-term storage and inventory management cost more
|
How to Choose the Right Model for Your Business
Choosing between both the approaches is a crucial decision. Cross-docking suits businesses that need fast delivery and less storage time. It works well for fast-moving items. Traditional warehousing is better for businesses requiring long-term storage. It offers better stock control and supports slower-moving products.
When choosing a model consider key factors like product, inventory turnover and costs. Cross-docking provides needed agility for fluctuating demand. It helps businesses respond quickly to customer needs. Traditional warehousing is better if you manage a diverse range of products that require longer storage. The right choice aligns logistics with business goals.
Real-world Use Cases
Walmart and Amazon use cross-docking. Walmart minimizes storage by transferring goods directly from inbound to outbound trucks. It reduces costs and improves efficiency. Helping them maintain competitive pricing. Amazon uses cross-docking in its fulfillment centers to speed up order processing. It ensures fast deliveries and higher customer satisfaction.
Most furniture retailers and seasonal brands prefer traditional warehousing. These businesses need large storage spaces. Especially during peak seasons. This helps them manage inventory efficiently. It also allows them to meet changing demand without immediate pressures of cross-docking.
Final Thoughts
The choice between the two approaches depends on business needs, logistics requirements and strategic goals. Cross-docking is fast and cost efficient. This makes it ideal for industries with high turnover and perishable goods. Traditional warehousing offers flexibility and stability. It is better for managing diverse inventory over time. Aligning logistics with business goals is essential to optimize efficiency and meet customer needs.
Using advanced logistics technologies like FarEye can further enhance your logistics strategies by providing real time visibility into supply chain processes. This enhances decision making for both the warehouse management practices. With such platforms, businesses gain agility to meet the market demands. They also ensure timely deliveries that meet customer expectations.
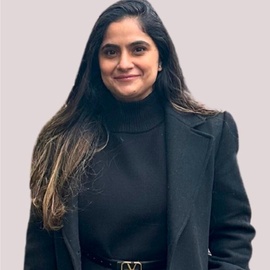
Komal Puri is a seasoned professional in the logistics and supply chain industry. As the AVP of Marketing and a subject matter expert at FarEye, she has been instrumental in shaping the industry narrative for the past decade. Her expertise and insights have earned her numerous awards and recognition. Komal’s writings reflect her deep understanding of the industry, offering valuable insights and thought leadership.