- Logistics
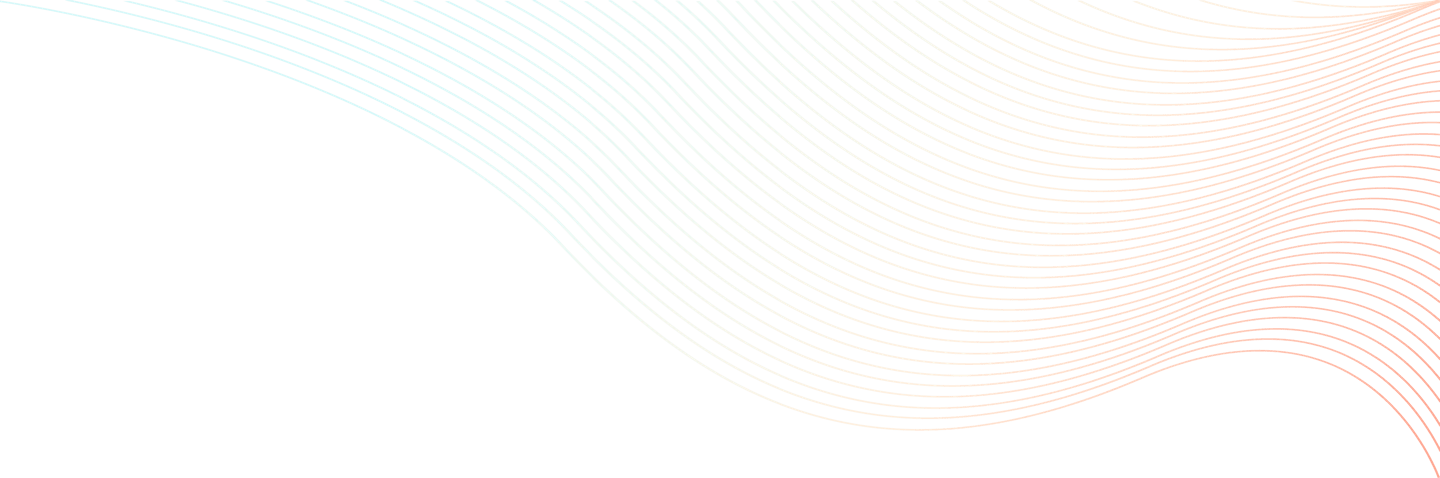
What is 3PL? Third-Party Logistics Complete Guide
Introduction to 3PL (Third-Party Logistics)
The modern supply chain is complex, requiring businesses to balance cost, speed, and efficiency while ensuring seamless operations. Many companies, instead of managing logistics in-house, turn to third-party logistics (3PL) providers to optimize their supply chain.
3PL logistics refers to outsourcing logistics operations to specialized service providers that manage various aspects of transportation, warehousing, distribution, and fulfillment. Whether it’s e-commerce, retail, or manufacturing, businesses rely on 3PL partners to streamline operations and focus on their core competencies.
What is 3PL?
Third-party logistics (3PL) refers to companies that provide outsourced logistics services, covering various aspects of supply chain management. These services may include:
- Warehousing: Storage and inventory management
- Transportation: Freight forwarding, last-mile delivery, and distribution
- Order Fulfillment: Picking, packing, and shipping orders
- Freight Brokerage: Facilitating seamless connections between shippers and carriers for optimized transportation efficiency.
- Reverse Logistics: Handling returns, recycling, and disposal
3PL providers serve as a bridge between businesses and carriers, delivering scalable logistics solutions that boost efficiency, lower costs, and enhance customer satisfaction. By leveraging 3PL services, businesses can optimize supply chains, meet fluctuating demand, and expand into new markets with ease.
Understanding 3PL Logistics
Third-party logistics (3PL) plays a crucial role in modern supply chains by helping businesses manage transportation, warehousing, and fulfillment. Outsourcing logistics to 3PL providers allows companies to concentrate on their core business while benefiting from the expertise, infrastructure, and technology of specialized logistics partners.
What is 3PL Logistics?
3PL logistics refers to outsourcing supply chain functions to specialized service providers. These providers manage various aspects of logistics, such as transportation, warehousing, distribution, and fulfillment, allowing businesses to scale operations without investing in in-house logistics infrastructure.
How 3PL Fits into the Supply Chain Ecosystem
The supply chain spans multiple stages, from raw material sourcing to last-mile delivery. 3PL providers bridge the gap between manufacturers, suppliers, retailers, and customers, delivering seamless logistics solutions that enhance supply chain efficiency.
Key ways 3PL enhances the supply chain include:
- Cost Reduction – Eliminating the need for in-house warehouses, fleet management, and logistics staff.
- Scalability – Adapting to fluctuations in demand, seasonal spikes, and new market expansions.
- Technology & Visibility – Providing real-time tracking, inventory management, and analytics.
- Global Reach – Enabling international shipping and cross-border logistics solutions.
3PL Terminology
Understanding logistics terminology is essential for working with 3PL providers. Below are some commonly used terms:
- FTL (Full Truckload): A shipment that occupies an entire truck, ensuring faster delivery without intermediate stops.
- LTL (Less Than Truckload): A shipment that shares truck space with other shipments, reducing costs but increasing transit time.
- WMS (Warehouse Management System): A software solution that manages inventory, order fulfillment, and warehouse operations.
- TMS (Transportation Management System): A software platform that optimizes shipping, tracking, and routing of freight.
- OMS (Order Management System): A system that handles order processing, tracking, and fulfillment across multiple sales channels.
- Last-Mile Delivery: The final stage of the delivery process where goods are transported from a distribution center to the end customer.
- Reverse Logistics: The management of product returns, repairs, and recycling to optimize resource recovery and efficiency.
3PL Services
3PL providers deliver a comprehensive range of logistics services designed to optimize business operations. These services include:
1. Transportation Services
- Freight Brokerage: Connecting shippers with carriers for efficient transport.
- Full Truckload (FTL) & Less Than Truckload (LTL) Shipping: Handling various shipment sizes.
- Intermodal Transport: Combining rail, road, sea, and air transport for cost-effective delivery.
- Last-Mile Delivery: Ensuring timely delivery to customers, especially for eCommerce.
2. Warehousing & Distribution
- Storage Solutions: Short-term and long-term warehousing.
- Inventory Management: Real-time tracking and stock control.
- Cross-Docking: Reducing storage requirements by directly transferring goods from inbound to outbound transportation for faster distribution.
3. Order Fulfillment
- Pick and Pack Services: Selecting items from inventory, packing, and preparing shipments.
- Kitting & Assembly: Bundling products before shipping.
- Returns Management (Reverse Logistics): Handling returned goods efficiently.
4. Freight Forwarding
- Customs Clearance: Managing documentation and compliance for international shipments.
- Cargo Insurance: Protecting shipments from loss or damage.
- Supply Chain Consultation: Helping businesses optimize global trade logistics.
Specialized 3PL Services
Certain industries require customized logistics solutions beyond standard transportation and warehousing. 3PL providers deliver specialized services tailored to unique logistics needs:
- Temperature-Controlled Logistics: Secure transport and storage of perishable goods, including food, pharmaceuticals, and medical supplies.
- Hazardous Materials Handling: Safe and compliant transportation of chemicals, flammable goods, and other regulated substances.
- White-Glove Delivery: Premium services that include product installation, setup, and handling of high-value items.
- E-commerce Fulfillment: Managing multi-channel fulfillment for online retailers, including integrations with marketplaces like Amazon and Shopify.
- Drop Shipping: Fulfilling orders by shipping products directly from the manufacturer or wholesaler to customers, eliminating the need for inventory storage.
- Project Logistics: Managing large-scale, complex shipments such as heavy machinery and industrial equipment.
How 3PL Services Work in Detail
Third-party logistics (3PL) providers streamline supply chain operations by handling everything from transportation and warehousing to order fulfillment and returns. Let’s explore how these services function in detail.
3PL eCommerce Platform Integration
With the rapid growth of eCommerce, 3PL providers integrate seamlessly with online platforms to enable efficient order fulfillment.
How 3PLs Integrate with eCommerce Platforms
3PLs use API-based integrations with major eCommerce platforms such as:
- Shopify
- Magento
- WooCommerce
- BigCommerce
- Amazon FBA (Fulfillment by Amazon)
This integration enables real-time synchronization of orders, inventory updates, and tracking details. When a customer places an order, the information is instantly relayed to the 3PL provider, who handles picking, packing, and shipping while updating the eCommerce store with tracking information.
Benefits of 3PL eCommerce Integration:
✔ Faster processing of orders
✔ Real-time inventory tracking
✔ Automated shipping label generation
✔ Streamlined returns management
Freight shipping is a core service offered by 3PLs, ensuring cost-effective transportation for businesses of all sizes.
Full Truckload (FTL) vs. Less-Than-Truckload (LTL)
FTL (Full Truckload) | LTL (Less Than Truckload) |
Uses the entire truck for one shipment | Shares truck space with shipments from multiple businesses |
Faster transit time (direct shipment) | Longer transit time (multiple stops for different deliveries) |
Best for high-volume shipments (10+ pallets) | Ideal for smaller shipments (1-10 pallets) |
Cost-effective for large shipments | Lower cost for small businesses shipping smaller loads |
Picking, Packing, and Shipping
Order fulfillment is a key function of 3PLs, ensuring precise product selection, secure packaging, and timely shipping to customers.
Step-by-Step 3PL Fulfillment Process
- Receiving Orders: Orders are automatically synced from eCommerce platforms.
- Picking: Warehouse staff picks the items from inventory using barcode scanners.
- Packing: Products are packed securely with appropriate materials (bubble wrap, boxes, etc.).
- Labeling: Shipping labels are generated and attached.
- Shipping: Orders are handed over to last-mile carriers (UPS, FedEx, DHL, etc.).
- Tracking & Customer Updates: Tracking numbers are sent to customers.
Advantages of 3PL Fulfillment Services:
✔ Faster order processing
✔ Reduced errors through automated systems
✔ Scalability during peak sales seasons
Kitting: Bundling and Assembly for Delivery
Kitting is a specialized fulfillment service where 3PLs assemble multiple items into pre-defined sets before shipping.
How 3PLs Handle Kitting:
- Pre-assembly of Products: Items are grouped together based on customer preferences.
- Custom Packaging: Bundled products are packed in branded or specialized packaging.
- Subscription Box Services: Many eCommerce brands use 3PL kitting for curated subscription boxes.
- Promotional Kits: Businesses running promotions may bundle products together with marketing materials.
Benefits of Kitting in 3PL:
✔ Faster fulfillment for bundled items
✔ Reduced shipping costs by consolidating multiple items
✔ Enhanced branding with custom packaging
Same-Day Shipping: How 3PLs Enable Faster Delivery
The demand for same-day and next-day shipping is rising, and 3PLs help businesses meet these expectations with:
- Strategic Warehousing: Placing inventory in multiple fulfillment centers closer to customers.
- Automated Order Processing: Ensuring rapid pick-and-pack services.
- Carrier Partnerships: Integrating with local couriers and last-mile delivery providers.
- Micro-Fulfillment Centers (MFCs): Small urban warehouses designed for rapid eCommerce fulfillment.
Same-day delivery is especially popular for retail, eCommerce, and perishable goods businesses looking to enhance customer satisfaction.
Inventory Management: Best Practices in 3PL
Efficient inventory management helps businesses maintain optimal stock levels, preventing both overstocking and stockouts.
How 3PLs Manage Inventory Efficiently:
- Real-Time Tracking: Leveraging Warehouse Management Systems (WMS) to monitor stock levels with accuracy and efficiency.
- ABC Analysis: Categorizing products based on demand (high, medium, low).
- Automated Replenishment: Reordering stock automatically when levels are low.
- Multi-Warehouse Distribution: Spreading inventory across multiple locations to reduce shipping time.
- Cycle Counting: Regularly auditing inventory to prevent discrepancies.
Benefits of 3PL Inventory Management:
✔ Reduced stockouts and overstock situations
✔ Optimized storage costs
✔ Faster order fulfillment
Reverse Logistics: Managing Returns, Repairs, and Recycling
Returns and exchanges are an integral aspect of logistics, with 3PLs playing a crucial role in efficiently managing reverse logistics.
How 3PLs Handle Returns:
- Return Initiation: Customers request a return through an online portal.
- Product Inspection: 3PLs assess returned items for resale, repair, or disposal.
- Refurbishment & Resale: If possible, returned products are repaired and restocked.
- Recycling & Disposal: Unusable items are recycled or disposed of responsibly.
- Refund Processing: Businesses issue refunds or replacements through the 3PL system.
Reverse Logistics is Crucial for:
✔ E-commerce retailers managing high return volumes
✔ Electronics brands handling repairs and refurbishments
✔ Sustainable brands reducing waste and improving recycling
3PL vs. Drop Shipping: Understanding the Differences
Both 3PL (Third-Party Logistics) and drop shipping are fulfillment models that help businesses manage logistics without handling inventory directly. However, they vary greatly in control, scalability, and cost structure. This section outlines the key differences, benefits, and drawbacks of each fulfillment method.
What is Drop Shipping?
Drop shipping is an order fulfillment method where retailers do not keep inventory on hand. Instead, when a customer places an order, the retailer forwards the order to a supplier, who then ships the product directly to the customer. The retailer never physically handles the product.
How Drop Shipping Works:
- A customer places an order on an online store.
- The retailer forwards the order details to the drop shipping supplier for processing.
- The supplier handles packaging and ships the product straight to the customer.
- The retailer earns a profit based on the price markup.
Drop shipping is popular in eCommerce businesses that want to start selling without investing in inventory or warehousing.
Drop Ship Order Fulfillment
Unlike 3PL order fulfillment, where businesses store inventory in a warehouse, drop shipping relies on suppliers to fulfill orders. This means:
- Retailers don’t handle picking, packing, or shipping.
- Orders are processed and fulfilled only after a purchase is made, eliminating the need for pre-stocked inventory.
- Delivery times are determined by the supplier's location and operational efficiency.
Drop shipping is commonly used for:
✔ Print-on-demand (custom apparel, accessories, and home décor)
✔ Low-cost general merchandise (gadgets, phone accessories, etc.)
✔ Seasonal products (holiday decorations, trending products)
Pros and Cons of Drop Shipping
Pros | Cons |
Low startup costs – Eliminates the need for investment in inventory or warehouse space. | Low profit margins – Suppliers take a significant cut, reducing profitability. |
Easy to start – Simple integration with platforms like Shopify, WooCommerce, and Amazon. | No inventory control – Businesses rely entirely on suppliers for product availability and quality. |
No warehouse management – Suppliers handle storage and shipping. | Slow shipping times – Many suppliers are overseas, leading to long delivery times. |
Scalability without inventory risk – Can test new products without purchasing stock. | Limited branding options – Suppliers control packaging, making custom branding difficult. |
Wide product variety – Sell products without pre-purchasing inventory. | High competition – Many drop shippers sell the same products, leading to price wars. |
3PL Order Fulfillment: How It Works
Unlike drop shipping, 3PL order fulfillment involves storing inventory in a third-party logistics provider’s warehouse, where they handle picking, packing, and shipping on behalf of a business.
How 3PL Fulfillment Works:
- Inventory Storage – Businesses send products to a 3PL warehouse.
- Order Processing – When an order is placed, the 3PL picks and packs the product.
- Shipping & Tracking – The 3PL manages order shipment through integrated carriers such as FedEx, UPS, and DHL.
- Returns Handling – 3PLs manage reverse logistics for returns and exchanges.
This model is widely used in eCommerce, retail, and B2B businesses looking to scale operations efficiently while maintaining control over branding and shipping speed.
Comparison: 3PL vs. Drop Shipping
Feature | Drop Shipping | 3PL (Third-Party Logistics) |
Inventory Ownership | No inventory required | Business owns and stores inventory |
Upfront Investment | Low (no need to buy stock) | Higher (buying inventory and paying for storage) |
Shipping Speed | Slower (depends on suppliers) | Faster (stock is held in regional warehouses) |
Profit Margins | Lower (suppliers take a big cut) | Higher (bulk purchasing reduces costs) |
Branding Control | Limited (supplier handles packaging) | Full control (custom packaging and inserts possible) |
Best for | Startups, new sellers, testing new products | Scaling businesses, established brands, fast fulfillment needs |
Benefits of Third-Party Logistics (3PL) Over Drop Shipping
- Faster Shipping – 3PLs operate fulfillment centers across different regions, allowing same-day and next-day delivery (unlike drop shipping, which often has long shipping times).
- Better Profit Margins – With bulk inventory purchasing, businesses can reduce per-unit costs, improving profitability.
- Branding & Customization – Businesses can add custom packaging, branded inserts, and marketing materials to create a unique customer experience.
- Scalability & Control – As businesses grow, 3PLs provide the infrastructure to handle high order volumes without supply chain bottlenecks.
- More Reliable Inventory Management – Unlike drop shipping, where stock is controlled by a supplier, 3PL partners allow businesses to track real-time inventory levels.
Key Differences Between Drop Shipping and 3PL for eCommerce
Factor | Drop Shipping | 3PL Fulfillment |
Warehousing | No warehouse needed | Requires 3PL storage |
Order Processing | Orders forwarded to supplier | Orders handled by 3PL |
Packaging Control | No control over packaging | Can use branded/custom packaging |
Shipping Speed | Slower (international suppliers) | Faster (local/regional warehouses) |
Returns Handling | Depends on supplier policies | Managed by the 3PL |
Business Model | Low-risk startup option | Best for businesses looking to scale |
Types of 3PL Providers
Third-party logistics (3PL) providers deliver varying service levels tailored to specific business requirements. While some only handle transportation and warehousing, others fully integrate into a company's supply chain. Understanding the various types of 3PL providers can help businesses choose the right partner.
1. Standard 3PL Providers
Basic logistics services such as transportation, warehousing, and distribution fall under standard 3PL providers. These companies handle the fundamental movement and storage of goods but do not provide additional value-added services.
Services Provided:
✔ Warehousing and inventory storage
✔ Transportation (FTL, LTL, freight forwarding)
✔ Order fulfillment (pick, pack, ship)
✔ Basic inventory tracking
Best for:
- Businesses needing simple logistics support
- Small to mid-sized eCommerce and retail companies
- Companies with in-house supply chain management
2. Service Developers (Value-Added 3PLs)
These 3PL providers go beyond standard logistics by offering value-added services such as custom packaging, labeling, kitting, and returns management. They help businesses streamline fulfillment while improving the customer experience.
Services Provided:
✔ Custom packaging & labeling
✔ Kitting and bundling
✔ Reverse logistics (returns & refurbishments)
✔ Freight consolidation and optimization
Best for:
- Businesses that want branded packaging and customized fulfillment
- eCommerce companies looking for enhanced customer experiences
- Brands that need specialized shipping solutions
3. Customer Adapters (Outsourced Logistics Management)
Customer Adapters take over a company’s logistics operations entirely, optimizing supply chain efficiency. They don’t offer new services but improve existing processes by managing transportation, inventory, and order fulfillment.
Services Provided:
✔ Full supply chain management
✔ Freight management & carrier negotiations
✔ Demand forecasting & inventory planning
✔ Cost optimization in logistics operations
Best for:
- Businesses looking to fully outsource logistics functions
- Companies that lack expertise in logistics management
- Mid-to-large enterprises needing supply chain optimization
4. Customer Developers (Fully Integrated 3PLs)
Customer Developers seamlessly integrate into a company's supply chain, overseeing all logistics operations. From procurement to last-mile delivery, they function as a strategic partner rather than merely a service provider.
Services Provided:
✔ End-to-end supply chain integration
✔ Direct coordination with manufacturers and suppliers
✔ AI-driven logistics optimization
✔ Custom IT solutions and logistics automation
Best for:
- Large enterprises with intricate supply chain requirements.
- Global businesses requiring full-scale logistics management
- Companies looking for long-term strategic logistics partnerships
5. Asset-Based vs. Non-Asset-Based 3PL Providers
3PL providers can be asset-based (owning warehouses, trucks, and fleets) or non-asset-based (operating through partnerships with carriers and warehousing companies).
Asset-Based 3PL Providers
These companies own and operate logistics assets such as warehouses, trucks, ships, and distribution centers.
Advantages:
✔ More control over shipments and inventory
✔ Cost savings on warehousing and fleet management
✔ Faster service with owned transportation networks
Disadvantages:
❌ Limited flexibility in partnering with external providers
❌ May not offer the lowest pricing options
Examples:
- FedEx Supply Chain
- DHL Supply Chain
- UPS Logistics
Non-Asset-Based 3PL Providers
These companies do not own logistics assets but work with multiple carriers, warehouses, and distribution networks to manage logistics.
Advantages:
✔ Greater flexibility in selecting carriers and partners
✔ Cost-effective by choosing the best market rates
✔ Ideal for companies with seasonal demand fluctuations
Disadvantages:
❌ Less direct control over shipping and warehousing
❌ Dependence on external partners can lead to delays
Examples:
- C.H. Robinson
- XPO Logistics
- Flexport
Choosing the Right Type of 3PL Provider
The right 3PL depends on your business size, needs, and logistics complexity.
Business Needs | Best 3PL Type |
Basic warehousing & transportation | Standard 3PL Providers |
Custom packaging & returns handling | Service Developers |
Full supply chain management | Customer Adapters |
End-to-end logistics operations | Customer Developers |
In-house warehousing & fleet | Asset-Based 3PL |
Flexible carrier & warehousing options | Non-Asset-Based 3PL |
For businesses that want flexibility and lower costs, non-asset-based 3PLs are ideal. If control and speed are priorities, asset-based 3PLs may be the better choice.
3PL vs. 4PL vs. 5PL: Understanding the Differences
As supply chain management evolves, businesses are moving beyond traditional third-party logistics (3PL) to fourth-party logistics (4PL) and fifth-party logistics (5PL). Each level of logistics management provides different degrees of control, integration, and strategic oversight.
1. 3PL (Third-Party Logistics): Tactical Logistics Partner
A 3PL (Third-Party Logistics) provider manages specific logistics operations like warehousing, transportation, and order fulfillment. Businesses outsource these functions to 3PLs for cost reduction and operational efficiency while still maintaining some control over their supply chain.
Key Roles of 3PLs:
✔ Transportation Management – Freight forwarding, FTL, LTL shipping
✔ Warehousing & Distribution – Storing inventory, picking, packing, and shipping
✔ Order Fulfillment – Processing eCommerce orders, handling returns
✔ Freight Brokerage – Coordinating shipping with third-party carriers
✔ Inventory Management – Monitoring stock levels and maximizing storage efficiency.
Example: A retailer outsources warehousing, order fulfillment, and shipping to a 3PL provider like DHL, FedEx, or XPO Logistics. The retailer still manages supplier relationships and customer service.
2. 4PL (Fourth-Party Logistics): Strategic Supply Chain Management
A 4PL (Fourth-Party Logistics) provider acts as a supply chain orchestrator, overseeing multiple 3PL providers and managing the entire logistics strategy. 4PLs do not own warehouses or trucks; instead, they coordinate and optimize all supply chain operations on behalf of the business.
Key Roles of 4PLs:
✔ End-to-End Supply Chain Integration – Managing multiple 3PLs, freight carriers, and suppliers
✔ Strategic Planning & Consulting – Optimizing supply chain efficiency
✔ Technology & Data Analytics – AI-driven logistics management, predictive analytics
✔ Freight & Vendor Management – Coordinating transportation providers, warehousing, and last-mile delivery
✔ Risk Management & Compliance – Ensuring regulatory compliance and minimizing supply chain disruptions
Example: A global electronics brand hires Accenture or Schneider Logistics (4PL providers) to fully manage their supply chain, from procurement to final delivery. The 4PL selects and oversees 3PL providers, freight companies, and warehousing solutions.
Difference from 3PL:
- 3PL executes logistics services (e.g., transportation, warehousing).
- 4PL designs, manages, and optimizes the entire supply chain, coordinating 3PLs.
3. 5PL (Fifth-Party Logistics): Digital Supply Chain & eCommerce Optimization
A 5PL (Fifth-Party Logistics) provider focuses on technology-driven supply chain solutions, aggregating demand across multiple clients and leveraging automation, AI, and big data to optimize logistics. 5PLs are popular in eCommerce, omnichannel fulfillment, and global logistics.
Key Roles of 5PLs:
✔ eCommerce Fulfillment Solutions – End-to-end digital supply chain management
✔ AI & Automation in Logistics – Predictive demand forecasting, automated warehouses
✔ Multi-Party Logistics Aggregation – Coordinating multiple 3PLs and 4PLs for cost efficiency
✔ Sustainable & Green Logistics – Optimizing routes and reducing carbon footprint
✔ Blockchain & IoT Integration – Enhancing supply chain transparency and security
Example: Amazon’s fulfillment network functions as a 5PL, utilizing AI, automation, and IoT to optimize global supply chain logistics across its network of warehouses, suppliers, and last-mile delivery providers.
Difference from 4PL:
- 4PL manages and optimizes a business’s logistics network.
- 5PL uses advanced technology to aggregate logistics demand and automate supply chain processes at a higher level.
Comparison: 3PL vs. 4PL vs. 5PL
Feature | 3PL (Third-Party Logistics) | 4PL (Fourth-Party Logistics) | 5PL (Fifth-Party Logistics) |
Focus | Operational logistics (warehousing, transportation, fulfillment) | Strategic supply chain management & consulting | AI-driven supply chain automation & aggregation |
Control | Business retains supply chain oversight | 4PL takes full control & manages 3PLs | 5PL automates & optimizes supply chains for multiple businesses |
Asset Ownership | Owns or partners with transportation & warehousing providers | No assets, manages multiple 3PLs | No assets, uses big data & AI for logistics coordination |
Technology Use | Basic warehouse & transport management systems | Advanced analytics & end-to-end supply chain software | AI, automation, blockchain, and IoT-based optimization |
Best for | Businesses needing logistics support for fulfillment & shipping | Enterprises looking for full supply chain management | eCommerce, large-scale global supply chain automation |
Benefits of 3PL Services
Outsourcing logistics to a Third-Party Logistics (3PL) provider can help businesses improve efficiency, reduce costs, and scale operations seamlessly. Whether you're a small eCommerce store or a global enterprise, 3PL services offer a strategic advantage in supply chain management.
1. Cost Efficiency: How 3PLs Reduce Operational & Logistics Costs
Handling logistics internally demands substantial investment in warehousing, fleet, workforce, and technology. 3PL providers help businesses cut these costs by offering shared logistics resources and economies of scale.
How 3PLs Reduce Costs:
✔ Lower Warehousing Expenses – Businesses avoid the cost of renting or building warehouses.
✔ Reduced Transportation Costs – 3PLs negotiate bulk shipping rates with carriers, passing savings to clients.
✔ No Need for Logistics Staff – Outsourcing eliminates hiring and training costs for logistics teams.
✔ Optimized Inventory Management – Reduces stock wastage and overstocking issues.
✔ Faster Delivery = Fewer Returns – Efficient fulfillment reduces order errors and returns.
Example: An eCommerce brand saves on warehousing and shipping costs by partnering with a 3PL instead of running its own fulfillment center.
2. Scalability and Flexibility: Adapting to Market Demands
As businesses grow, logistics needs change. A 3PL provides the flexibility to scale operations up or down based on demand fluctuations.
How 3PLs Enable Scalability:
✔ Handles Seasonal Peaks – Supports high-order volumes during Black Friday, holidays, and sales periods.
✔ Multiple Fulfillment Centers – Expands warehouse locations as the business grows.
✔ On-Demand Storage – Uses shared warehouse space, avoiding fixed storage costs.
✔ Adapts to Market Changes – Businesses can enter new markets without setting up logistics infrastructure.
Example: A fashion retailer using a 3PL network can scale fulfillment during peak shopping seasons without needing extra staff or warehouses.
3. Access to Expertise: Leveraging 3PL Industry Knowledge
Logistics is complex, and 3PL providers bring decades of experience in optimizing supply chains. Businesses benefit from their expertise in:
✔ Freight Management – Selecting the best shipping methods (FTL, LTL, intermodal).
✔ Customs & Compliance – Handling international shipping regulations.
✔ Route Optimization – Reducing delivery times and fuel costs.
✔ Returns Management – Improving customer experience through seamless returns processing.
Example: A company expanding globally avoids customs delays by relying on a 3PL with expertise in international shipping regulations.
4. Improved Technology: Access to Advanced Logistics Software
Investing in warehouse management systems (WMS), transportation management systems (TMS), and AI-driven analytics is expensive. 3PLs offer access to these technologies without requiring businesses to invest in them directly.
Key 3PL Technologies:
✔ Warehouse Management Systems (WMS) – Tracks inventory in real-time.
✔ Transportation Management Systems (TMS) – Optimizes shipping and route planning.
✔ AI & Predictive Analytics – Forecasts demand and prevents stockouts.
✔ IoT & RFID Tracking – Ensures real-time shipment visibility.
Example: An eCommerce brand uses a 3PL’s real-time tracking system to provide customers with accurate delivery updates.
5. 3PL Service and eCommerce Growth: Supporting Online Retail Expansion
With online shopping booming, eCommerce businesses need fast, efficient fulfillment. 3PLs help brands meet high customer expectations by ensuring:
✔ Faster Order Processing – Orders are picked, packed, and dispatched on the same day.
✔ Multiple Warehouse Locations – Reduces shipping times by storing inventory closer to customers.
✔ Last-Mile Delivery Optimization – Partners with couriers for same-day and next-day shipping.
✔ Returns Handling – Simplifies reverse logistics for a smooth customer experience.
Example: Amazon FBA (a 3PL service) allows sellers to scale globally by handling fulfillment, customer service, and returns.
How to Find the Best 3PL Providers
Choosing the right Third-Party Logistics (3PL) provider is critical to ensuring efficient supply chain operations, faster deliveries, and cost savings. The ideal 3PL partner should align with your business goals, industry needs, and customer expectations.
1. 3PL Services Expertise: What to Look for in a 3PL Provider
Not all 3PL providers offer the same level of expertise. When evaluating potential partners, consider their:
✔ Core Services – Do they offer warehousing, fulfillment, freight management, and last-mile delivery?
✔ Industry Experience – Have they worked with businesses in your industry (e.g., retail, food, electronics)?
✔ Scalability – Can they support business growth, seasonal peaks, and multi-location fulfillment?
✔ Technology Integration – Do they offer API-based integrations with Shopify, Amazon, and ERP systems?
✔ Track Record – Check case studies, reviews, and references from other clients.
Example: If you're an eCommerce brand, you need a 3PL with expertise in high-volume fulfillment, same-day shipping, and seamless Shopify/Amazon integration.
2. 3PL Warehouse Locations: Importance of Distribution Centers
The location of 3PL warehouses directly impacts shipping costs, delivery times, and overall efficiency.
Why Warehouse Locations Matter:
✔ Faster Shipping – Inventory stored near customers reduces transit times.
✔ Lower Shipping Costs – Strategically placed fulfillment centers cut down on long-distance shipping expenses.
✔ Multi-Channel Fulfillment – A distributed warehouse network ensures efficient omnichannel fulfillment.
What to Look for in Warehouse Locations:
✅ Proximity to your primary customer base (e.g., U.S. East vs. West Coast, Europe, Asia)
✅ Locations near major shipping hubs, airports, and seaports
✅ Multiple warehouses for regional fulfillment and reduced last-mile delivery costs
Example: A U.S.-based eCommerce store with customers nationwide benefits from 3PL warehouses on both the East and West Coasts to reduce shipping time and costs.
3. 3PL Customer Support: How it Impacts Your Business
Reliable customer support is essential for a smooth logistics operation. Poor communication and delays can disrupt order fulfillment and impact customer satisfaction.
Key Aspects of Strong 3PL Customer Support:
✔ Dedicated Account Manager – A single point of contact for problem resolution.
✔ Real-Time Support – 24/7 support for urgent logistics issues.
✔ Technology & Tracking Transparency – Ability to monitor shipments, inventory, and returns in real-time.
✔ Flexibility in Handling Issues – Fast response to order errors, lost shipments, and demand fluctuations.
Example: A business facing high order volumes during peak seasons needs a 3PL with responsive support to avoid delays and manage exceptions efficiently.
4. Specialty 3PL Services: Finding a Niche Logistics Partner
Some industries require specialized logistics solutions beyond standard warehousing and fulfillment.
Key Niche 3PL Services to Consider:
Specialty Service | Best for Industries | What to Look For |
Cold Chain Logistics | Food, Pharmaceuticals, Perishables | Temperature-controlled storage, real-time monitoring |
Hazardous Materials Handling | Chemicals, Electronics, Healthcare | Certified hazmat transportation, compliance with regulations |
White-Glove Delivery | Luxury Goods, Furniture, Electronics | Special handling, assembly, and in-home setup |
Reverse Logistics | eCommerce, Retail | Efficient returns management, refurbishment services |
Cross-Border Logistics | Global Brands, Import/Export | Customs clearance, duty optimization, international tracking |
Resources to Help Evaluate 3PLs
Selecting the right Third-Party Logistics (3PL) provider requires thorough evaluation of security, costs, shipping efficiency, and omnichannel integration. Here are key factors and resources to help assess a 3PL’s effectiveness.
1. 3PL Security and Operational Continuity
A reliable 3PL provider should have strong security measures to protect data, inventory, and operations. Assess the following:
How to Evaluate 3PL Security & Business Continuity:
✔ Data Security & Compliance – Does the 3PL comply with GDPR, ISO 27001, or SOC 2 for data protection?
✔ IT Infrastructure & Cybersecurity – Does it use firewalls, encrypted transactions, and secure API integrations?
✔ Disaster Recovery Plan – What happens if a warehouse experiences a fire, flood, or cyberattack?
✔ Inventory Security Measures – Are warehouses equipped with CCTV, restricted access, and theft prevention?
✔ Business Continuity Plan (BCP) – How does the 3PL ensure uninterrupted service during disruptions?
Example: A retailer working with a 3PL should ensure data encryption, warehouse surveillance, and backup inventory plans to avoid losses.
2. Inventory and Order Fulfillment Costs: Key Metrics for Cost-Effectiveness
Key Inventory & Fulfillment Metrics:
✅ Storage Costs – How much does the 3PL charge for shelf space, pallet storage, and SKU management?
✅ Pick & Pack Fees – What are the per-order costs for picking and packing items?
✅ Receiving Fees – Does the 3PL charge for stocking and restocking inventory?
✅ Minimum Monthly Fees – Are there fixed monthly fees, even during slow sales periods?
✅ Return Processing Fees – How much does the 3PL charge for handling returns and exchanges?
Example: A business with high SKU turnover should select a 3PL with low storage fees and fast order processing rates to optimize costs.
3. Shipping Costs: Hidden Fees & Freight Optimization
Shipping is a major cost factor. Many 3PLs have hidden fees that impact the total logistics budget.
How to Optimize 3PL Shipping Costs:
✔ Understand Carrier Markups – Some 3PLs charge extra for shipping beyond carrier rates.
✔ Negotiate Bulk Discounts – Ask if they provide volume-based shipping discounts.
✔ Analyze Zone-Based Shipping – Warehouses closer to customers reduce zone-based surcharges.
✔ Look for Fuel Surcharges – Check for fuel price fluctuations and additional handling fees.
✔ Compare Small Parcel vs. Freight Costs – Determine if LTL (Less Than Truckload) or FTL (Full Truckload) saves money.
Example: A 3PL with multi-warehouse distribution can lower shipping costs by reducing zone-based fees and last-mile delivery charges.
4. Omnichannel Integrations: Seamless Multi-Channel Fulfillment
Modern businesses sell across multiple platforms (eCommerce, retail, marketplaces, social commerce). A 3PL must offer omnichannel integration to manage inventory and fulfillment seamlessly.
Essential 3PL Omnichannel Integrations:
✅ eCommerce Platforms – Shopify, Magento, WooCommerce, BigCommerce
✅ Marketplaces – Amazon, eBay, Walmart, Etsy
✅ Retail & B2B Fulfillment – ERP integrations with NetSuite, SAP, Microsoft Dynamics
✅ Social Commerce – Facebook Shops, Instagram, TikTok
✅ Shipping & Tracking Software – FedEx, UPS, DHL, USPS integrations
Example: An apparel brand selling on Shopify, Amazon, and TikTok needs a 3PL with real-time inventory sync to avoid stockouts across platforms.
Challenges of Working with 3PLs
While Third-Party Logistics (3PL) providers offer significant benefits, businesses often face challenges related to control, costs, service reliability, and technology gaps. Understanding these challenges and how to manage them can help ensure a smooth logistics partnership.
1. Loss of Control: Managing Communication & Oversight Challenges
Outsourcing logistics means businesses rely on an external partner to handle inventory, fulfillment, and shipping. This can lead to issues such as:
- Limited Visibility – Not having real-time control over warehouse operations.
- Delayed Communication – Slow responses to order issues, stockouts, or shipment problems.
- Quality Control Issues – Inconsistent packaging, wrong shipments, or inventory mismanagement.
How to Manage This Challenge:
✔ Use 3PLs with Real-Time Tracking – Choose providers offering inventory and order visibility through dashboards.
✔ Set Clear KPIs – Establish service level agreements (SLAs) for order accuracy, delivery time, and stock management.
✔ Have a Dedicated Account Manager – A single point of contact at the 3PL improves response times and accountability.
Example: A retailer using a 3PL with API-based inventory tracking ensures they can monitor stock levels in real-time and prevent stockouts.
2. Cost Overruns: Identifying & Avoiding Hidden Fees
Many businesses underestimate the true costs of outsourcing logistics, leading to unexpected expenses such as:
- Storage Overages – Higher fees for exceeding warehouse space.
- Peak Season Surcharges – Increased fulfillment costs during high-demand periods.
- Order Processing Fees – Additional costs for pick and pack services beyond standard rates.
- Return Handling Charges – Extra fees for reverse logistics and restocking.
- Shipping Rate Markups – Some 3PLs inflate carrier shipping costs.
How to Manage This Challenge:
✔ Request a Detailed Cost Breakdown – Ensure all storage, fulfillment, and shipping fees are transparent before signing a contract.
✔ Negotiate Volume Discounts – Some 3PLs offer bulk order processing and shipping discounts.
✔ Use Predictive Analytics – Demand forecasting helps avoid last-minute fulfillment cost spikes.
Example: An eCommerce brand planning for holiday season demand should negotiate seasonal pricing in advance to avoid unexpected surcharges.
3. Service Reliability: Measuring & Managing 3PL Performance
If a 3PL fails to meet service expectations, businesses face delayed shipments, inaccurate orders, and poor customer experiences.
Common 3PL Service Issues:
- Late Deliveries – Orders consistently missing promised delivery times.
- Inventory Mismanagement – Stock discrepancies causing stockouts or overstocking.
- Poor Returns Handling – Slow or unorganized reverse logistics processes.
- Lack of Flexibility – Inability to scale during peak demand periods.
How to Manage This Challenge:
✔ Define SLAs & Performance Metrics – Track KPIs like on-time delivery rate, order accuracy, and warehouse processing speed.
✔ Use a Performance Dashboard – A 3PL with real-time data tracking allows businesses to monitor logistics performance.
✔ Have a Backup Plan – Diversify logistics partners in case a 3PL underperforms.
Example: A subscription box company tracks monthly fulfillment accuracy and switches 3PLs if error rates exceed 5%.
4. Technology Gaps: Ensuring Your 3PL is Tech-Savvy
A 3PL without advanced logistics technology can cause inefficiencies, inaccurate inventory tracking, and poor data integration.
Technology Challenges with 3PLs:
- Lack of Real-Time Tracking – No visibility into inventory levels or shipping status.
- Poor Integration – Incompatibility with eCommerce platforms (Shopify, Amazon, Magento, etc.).
- Limited Data Analytics – No predictive demand forecasting or AI-driven optimization.
- Manual Processes – Paper-based order processing slows fulfillment.
How to Manage This Challenge:
✔ Ensure API Integration – Choose a 3PL that integrates with your order management and ERP systems.
✔ Use AI & Predictive Analytics – Advanced 3PLs offer automated demand forecasting and warehouse optimization.
✔ Check Mobile & Cloud Capabilities – A 3PL with mobile tracking and cloud-based WMS (Warehouse Management System) improves efficiency.
Example: An online retailer uses a 3PL with AI-based demand forecasting to prevent stockouts during peak sales events.
Future Trends in 3PL
The Third-Party Logistics (3PL) industry is rapidly evolving with advancements in automation, artificial intelligence (AI), sustainability, and blockchain technology. These innovations are reshaping warehousing, transportation, and supply chain visibility, making logistics more efficient, cost-effective, and environmentally friendly.
1. Automation & Robotics in Warehousing
Robots and automation are transforming 3PL warehouses, making order fulfillment faster, more accurate, and less labor-intensive.
Key Innovations in Warehouse Automation:
✅ Autonomous Mobile Robots (AMRs) – Robots like those from Locus Robotics and Geek+ assist with picking and packing.
✅ Automated Storage & Retrieval Systems (AS/RS) – AI-powered robotic systems 2. AI & Data Analytics in Logistics with precision.
✅ Drones for Inventory Management – Drones perform real-time inventory audits and reduce stock discrepancies.
✅ Conveyor & Sorting Systems – High-speed automated sorting improves package routing efficiency.
Example: Amazon and DHL use robotic arms and AI-driven sorting systems to process thousands of orders per hour with minimal human intervention.
2. AI & Data Analytics in Logistics
AI-powered predictive analytics and machine learning help 3PLs optimize routing, demand forecasting, and warehouse efficiency.
How AI is Transforming 3PL Logistics:
✔ Predictive Demand Forecasting – AI predicts inventory needs based on market trends and past data.
✔ Dynamic Route Optimization – AI-powered logistics platforms like FarEye optimize delivery routes in real-time.
✔ Chatbots & AI Customer Support – AI-driven chatbots assist with shipment tracking and customer inquiries.
✔ Automated Freight Matching – AI analyzes carrier availability and cost trends to match shipments with the best freight providers.
3. Green Logistics & Sustainability in 3PL
The logistics industry is a major contributor to carbon emissions, and 3PL providers are adopting eco-friendly initiatives to reduce their environmental impact.
Sustainable Trends in 3PL:
✅ Electric & Hydrogen-Powered Vehicles – DHL and FedEx are investing in EV fleets for last-mile delivery.
✅ Carbon Offset Programs – Companies like Maersk offer carbon-neutral shipping options.
✅ Eco-Friendly Warehouses – Solar-powered fulfillment centers reduce energy consumption.
✅ Sustainable Packaging – 3PLs use biodegradable materials and recycled packaging to reduce waste.
4. The Role of Blockchain in 3PL
Blockchain technology is revolutionizing supply chain transparency and security, making freight tracking and contract execution more reliable.
How Blockchain is Used in 3PL:
✔ Real-Time Shipment Tracking – Blockchain enables tamper-proof tracking of shipments across borders.
✔ Smart Contracts – Automated blockchain contracts ensure timely payments and secure transactions.
✔ Fraud Prevention – Verifies the authenticity of shipments and prevents counterfeiting.
✔ End-to-End Visibility – Provides a single source of truth for suppliers, 3PLs, and retailers.
Example: IBM and Maersk’s TradeLens platform uses blockchain to streamline international shipping, reducing delays and paperwork.
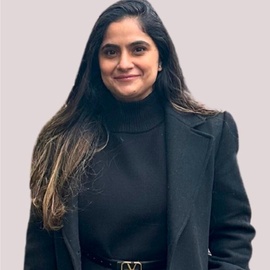
Komal Puri is a seasoned professional in the logistics and supply chain industry. As the AVP of Marketing and a subject matter expert at FarEye, she has been instrumental in shaping the industry narrative for the past decade. Her expertise and insights have earned her numerous awards and recognition. Komal’s writings reflect her deep understanding of the industry, offering valuable insights and thought leadership.
Let's Talk to Our Experts and Optimize Your Deliveries Today!
An expert from our team will reach out within 24 hours