- Returns Management
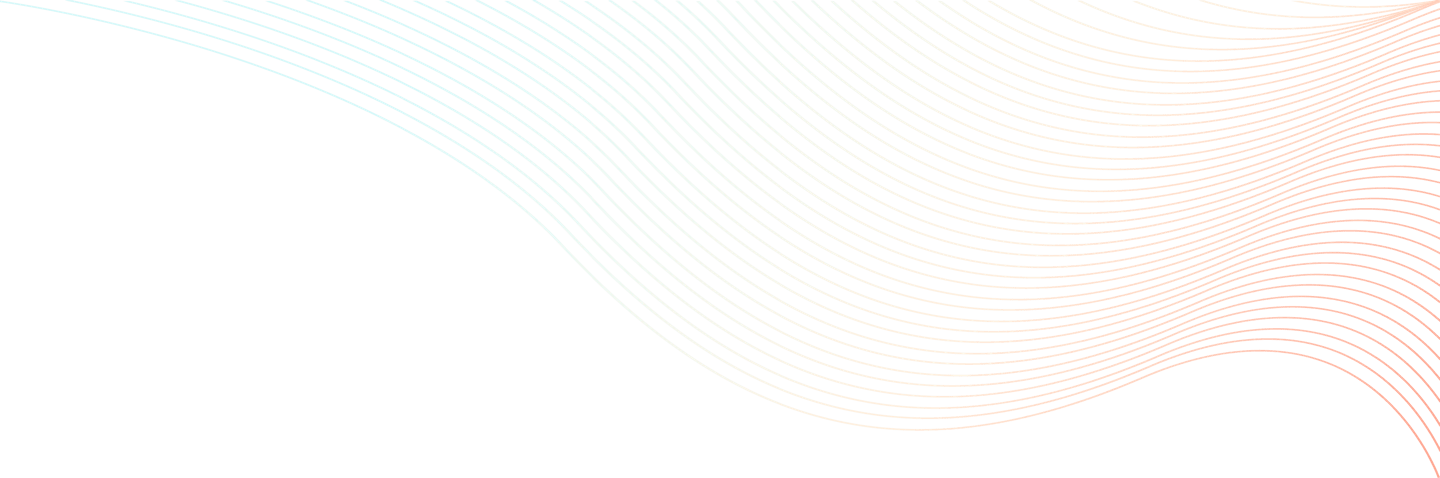
What is reverse logistics? Complete Guide to Reverse Logistics
Reverse logistics encompasses the journey of products from consumers back to manufacturers, encompassing returns, repairs, recycling, and more. Discover how this intricate process works, from initial tracking to final disposition. We'll navigate through the challenges businesses face in managing returns and excess inventory while highlighting innovative solutions to optimize efficiency and minimize costs. Whether you're seeking insights into streamlined operations or sustainable practices, our blog will guide you through the dynamic landscape of reverse logistics, where challenges are turned into opportunities.
What is reverse logistics?
Reverse logistics refers to the process of moving goods from their final destination back to the manufacturer or distributor for purposes such as returns, repairs, refurbishing, recycling, or disposal. Unlike traditional (forward) logistics, which focuses on getting products to customers, reverse logistics manages the flow of goods back through the supply chain.
Historically, early 20th-century supply chain management mainly focused on production and distribution, with little emphasis on returns. However, as consumer markets grew and industries expanded, particularly post-World War II, managing returned goods, defective products, and recycling became more important, laying the foundation for reverse logistics.
Reverse logistics evolved from traditional logistics as companies faced increasing returns, recalls, and waste management demands. Today, it includes:
- Returns Management: Handling product returns for resale or disposal.
- Refurbishment and Remanufacturing: Repairing products for resale.
- Recycling and Waste Disposal: Processing end-of-life products for recycling or safe disposal.
Why Reverse Logistics is Critical in the Modern Supply Chain
Reverse logistics has become increasingly important due to several key factors:
1. Economic Factors:
- Cost Recovery: Companies can recover value by reselling, refurbishing, or recycling returned products instead of discarding them. Efficient reverse logistics helps recapture revenue and reduce losses.
- Inventory Management: Managing returns effectively reduces excess inventory and avoids stockpile waste, leading to better cash flow and optimized storage costs.
- Product Recalls: In cases of defective products, effective reverse logistics minimizes the financial impact of recalls by streamlining the process of recovering faulty goods.
2. Environmental Factors:
- Sustainability: Growing environmental concerns have pushed companies to adopt circular supply chains, where reverse logistics plays a critical role in recycling, reducing waste, and reusing materials. This aligns with global efforts toward reducing carbon footprints and promoting eco-friendly business practices.
- Regulatory Compliance: Stricter environmental regulations require businesses to manage e-waste and end-of-life products responsibly, making reverse logistics essential for compliance.
3. Consumer-Driven Factors:
- Rising Returns from eCommerce: With the explosion of online shopping, return rates have increased significantly. Efficient reverse logistics ensures smooth returns, enhancing customer satisfaction and brand loyalty.
- Customer Expectations: Today’s consumers expect hassle-free, fast, and sometimes free returns. Meeting these demands requires robust reverse logistics systems that can handle high return volumes without compromising service quality.
Forward vs. Reverse Logistics
Flowchart Comparison:
- Forward Logistics:
- Manufacturer → Distributor → Retailer → Customer
- Focuses on production, distribution, and delivery of products to end consumers.
- Reverse Logistics:
- Customer → Retailer → Distributor → Manufacturer (for return, repair, or recycling)
- Involves moving products backward in the supply chain for returns, repairs, or disposal.
Operational Complexities:
- Costs: Reverse logistics can be more expensive due to product inspection, repair, restocking, or recycling costs. Return handling often lacks the economies of scale found in forward logistics.
- Infrastructure: Forward logistics benefits from streamlined, established systems. Reverse logistics requires specialized processes for returns, including collection points, inspection centers, and refurbishment facilities.
- Time: Processing returns is often slower, involving detailed inspections, sorting, and sometimes complex repairs or recycling steps, unlike forward logistics where the focus is on speed-to-market.
Impact on Customer Service and Lifecycle Management:
- Customer Service: Reverse logistics directly impacts customer satisfaction through hassle-free returns, refunds, and exchanges. A strong reverse logistics system improves brand loyalty and customer retention.
- Lifecycle Management: It supports extended product lifecycle by enabling repairs, refurbishment, and recycling, helping companies reduce waste and contribute to sustainable practices.
Evolution of Reverse Logistics
The Origins of Reverse Logistics
- Reverse logistics has roots in early industrial practices, where managing returns and repairs was informal, often handled locally. During the Industrial Revolution, logistics systems began to formalize as industries grew and transportation networks expanded.
- World War innovations greatly influenced logistics, especially in managing surplus materials, faulty equipment, and returned goods. Military supply chains needed to handle repairs and redistribution, laying the groundwork for reverse logistics principles.
Pre-Globalization Era
- Before globalization, product returns and repairs were mostly localized, with manufacturers handling defective or unwanted products within regional markets. The scale and complexity of reverse logistics were minimal, focused on individual customer returns and limited remanufacturing.
Post-War Globalization and Supply Chain Expansion
- After World War II, global supply chains grew, increasing the complexity of reverse logistics. Products were being manufactured, sold, and returned across borders, making it more difficult to track returns, manage defects, and handle waste disposal. This expansion required companies to rethink reverse logistics, as it now involved international coordination, higher costs, and stricter regulations for returns and recycling across different markets.
The Rise of eCommerce and Reverse Logistics
The 1990s-2000s internet boom marked a major turning point for reverse logistics. With the rapid rise of eCommerce platforms like Amazon and eBay, consumer behavior shifted towards online shopping, leading to higher volumes of product returns. Unlike traditional brick-and-mortar retail, where customers could inspect products before purchase, online shoppers faced greater uncertainty about product quality, size, and fit, resulting in increased returns.
This surge in returns posed new challenges for reverse logistics:
- Higher Return Rates: Online purchases have significantly higher return rates (up to 30% for some sectors like fashion), compared to in-store purchases.
- Complex Return Processes: Companies had to establish more efficient reverse logistics networks to handle shipping, product inspection, repackaging, and restocking across wider geographic areas.
- Cost Management: Managing returns became costly, as companies needed to process returned goods, refurbish or dispose of them, and handle the associated logistics, often eating into profit margins.
- Customer Expectations: Consumers began expecting hassle-free return policies, such as free returns, faster processing, and easy-to-use return systems, forcing businesses to improve their reverse logistics capabilities.
Technological Impact on Reverse Logistics (2010s - Present)
Reverse Logistics Software in Streamlining Returns and Recalls
- Advanced Reverse Logistics software has revolutionized reverse logistics by automating and optimizing returns and recall processes. Companies can now track returned products in real time, manage inventory, process refunds faster, and handle recalls efficiently. This technology reduces errors, speeds up product assessments, and enhances customer satisfaction through streamlined reverse flows.
Future Evolution: The Circular Economy and Reverse Logistics
- With growing consumer demand for sustainable practices, companies are rethinking reverse logistics to align with the circular economy—a model that focuses on reducing waste by reusing, refurbishing, and recycling products. Reverse logistics plays a crucial role in this by enabling the return of used products for remanufacturing, recycling, or resale. This shift towards sustainability is driving businesses to create closed-loop supply chains, minimizing environmental impact and supporting long-term resource conservation.
Reverse Logistics for Different Business Models
B2B Reverse Logistics (e.g., Bulk Product Recalls):
- In B2B settings, reverse logistics often involves large-scale returns, such as bulk product recalls or returns from distributors and retailers.
- Complexity: B2B reverse logistics is usually more complex due to higher volumes, stricter contractual obligations, and potential recalls involving entire product lines.
- Focus: It emphasizes efficiency in recalling, refurbishing, or recycling large quantities, with a strong emphasis on maintaining business relationships, compliance, and cost recovery.
B2C Reverse Logistics (eCommerce Returns Management):
- In B2C, reverse logistics mainly focuses on managing individual returns from consumers, especially in eCommerce where return rates are higher.
- Challenges: Handling high volumes of small returns, offering free or fast returns, and ensuring customer satisfaction through hassle-free return processes.
- Focus: Customer-centric, aiming for quick returns processing, refund handling, and restocking, all while minimizing costs and maintaining a seamless customer experience.
How does reverse logistics management work?
Reverse logistics management involves a series of processes and activities aimed at managing the movement of products from consumers back to the manufacturer or retailer for various purposes, including returns, repairs, recycling, and more. Here is a general outline of the process involved in reverse logistics:
Product Returns: Customers initiate the process by returning products for various reasons, such as defects, dissatisfaction, or incorrect orders. The returned items may range from individual items to bulk shipments.
Collection and Sorting: Returned products are collected from different sources, such as retail stores, distribution centers, or directly from customers. They are then sorted based on their condition and reason for return. This step helps determine whether products can be resold, repaired, recycled, or need to be disposed of.
Assessment and Refurbishing: Returned items that are in good condition may undergo assessment, refurbishing, or reconditioning to bring them back to a saleable state. This can involve cleaning, repairing, repackaging, or updating the product to meet quality standards.
Disposition Decision: Depending on the condition of the returned items, a decision is made about their next steps. Products that can be resold might be reintroduced to inventory, while those requiring repairs may go through rework processes. Items that cannot be resold might be dismantled for parts or materials, or sent for recycling or disposal.
Recycling and Disposal: Products that are beyond repair or cannot be resold are directed toward recycling or disposal.Recycling includes the retrieval of valuable components or materials, whereas ensuring proper disposal maintains conformity with environmental regulations.
Transportation: Products move through various stages of reverse logistics using transportation methods similar to those in traditional logistics. Items may be transported to refurbishing facilities, recycling centers, or disposal sites.
Tracking and Visibility: Just like traditional logistics, tracking and visibility are crucial in reverse logistics. This allows companies to monitor the status and location of returned items, ensuring efficient processing and reducing the chances of lost or mismanaged products.
Data Analysis and Continuous Improvement: Companies analyze data related to returns, disposition outcomes, costs, and customer feedback. This analysis informs improvements in processes, customer service, and decision-making to enhance overall reverse logistics efficiency.
Types of reverse logistics
Reverse logistics covers a range of processes and actions centered on moving products in the opposite direction of the conventional supply chain. Here are some primary categories within reverse logistics:
Product Returns: This is one of the most common forms of reverse logistics. Customers initiate product returns for diverse reasons, including defects, damage, dissatisfaction, or erroneous orders. Efficiently managing returned items is crucial to upholding customer satisfaction. Companies need to determine whether returned items can be resold, refurbished, or need to be discarded.
Remanufacturing and Refurbishing: Remanufacturing involves disassembling returned products, replacing worn-out or faulty parts, and reassembling them into like-new condition. Refurbishing is a less extensive process that involves repairing and improving the cosmetic appearance of products. Both approaches enable businesses to prolong the lifespan of products and regain their value.
Repair and Warranty Services: Companies often provide repair services for products that develop issues after purchase, especially those under warranty. Efficient reverse logistics ensure that defective items are collected, repaired, and returned to customers promptly. This process helps uphold product quality and customer loyalty.
Recycling and Material Recovery: Recycling focuses on disassembling products to recover valuable materials such as metals, plastics, and electronic components. These materials possess the potential for reuse in crafting new products, thereby lessening the need for fresh resources and mitigating environmental repercussions. Electronics, appliances, and automotive parts are common items targeted for recycling.
Product Redistribution: Unsold or excess inventory can be returned to manufacturers or redistributed to other markets or stores where demand exists. This process helps optimize inventory levels, reduce waste, and ensure that products are utilized effectively.
Management of Hazardous Materials: Specific products like chemicals, batteries, and electronic waste necessitate particular treatment due to environmental rules and potential dangers. Reverse logistics guarantees the proper collection, transportation, and disposal of these items, all in accordance with legal and environmental criteria.
End-of-Life Management: This entails the appropriate disposal of items that have reached the conclusion of their functional lifespan. Proper disposal methods, such as incineration or landfilling, are employed to minimize environmental impact and adhere to regulatory requirements.
Recall Management: In the event of product recalls due to safety concerns or defects, reverse logistics plays a vital role in collecting the affected products, identifying the root cause, implementing corrective actions, and managing customer communications.
Lease and Rental Returns: In industries like automotive and equipment leasing, reverse logistics involves the collection, inspection, and refurbishing of leased or rented items before returning them to inventory or releasing them to new customers.
What are the five 5 R's of Reverse logistics?
The "5 R's" of reverse logistics are a set of principles that guide sustainable and efficient management of products at the end of their lifecycle. These principles correspond with the ideology of the circular economy, which seeks to diminish waste and amplify resource value. The 5 R's in the realm of reverse logistics include:
Returns: The first "R" represents the process of managing returned products. This includes handling customer returns, warranty claims, and defective items. Efficient returns management involves assessing the condition of returned products and determining whether they can be resold, refurbished, or need to be disposed of.
Remanufacturing: The second "R" refers to remanufacturing, which involves disassembling returned or used products, replacing worn-out or faulty components, and reassembling them to be as good as new. This procedure lengthens the lifespan of products and lessens the requirement for fresh raw materials.
Refurbishing: Refurbishing, the third "R," is a less intensive process than remanufacturing. It involves repairing and improving the appearance of products to make them suitable for resale. This approach can be applied to products with minor defects or cosmetic issues.
Reuse: The fourth "R" emphasizes the practice of reusing products or components that still have value. This could involve repurposing products for a different use, utilizing components in new products, or finding alternative markets for products that are still functional.
Recycling: The fifth "R" stands for recycling, which involves dismantling products to recover valuable materials such as metals, plastics, and electronics. The utilization of these materials facilitates the generation of new products, thereby lowering the necessity for untouched resources and mitigating environmental effects.
What is reverse Logistics tracking?
Reverse Logistics Tracking refers to the process of monitoring and tracing the movement and status of products as they undergo various reverse logistics activities, such as returns, repairs, refurbishing, recycling, or disposal. This tracking helps businesses maintain visibility into the reverse logistics chain, enabling them to make informed decisions, optimize processes, enhance customer satisfaction, and ensure compliance with regulations.
Modern technologies, such as RFID (Radio Frequency Identification), barcodes, GPS, and software platforms, play a pivotal role in facilitating efficient reverse logistics tracking by capturing real-time data and providing insights into the journey of returned items.
Example of reverse logistics
Here's an example of reverse logistics in action:
Example: Refurbishment and Recycling of Electronics
Visualize a company within the realm of consumer electronics, engaged in the manufacturing and marketing of smartphones. As part of their commitment to sustainability, the company has a well-established reverse logistics system in place to manage returned and end-of-life smartphones.
Product Returns: Customers occasionally return smartphones due to defects, malfunctions, or upgrades. These returned devices are collected from retail stores or through mail-in programs.
Assessment: Upon receiving returned smartphones, the company assesses each device to determine its condition. Some devices might have minor issues that can be repaired, while others might be beyond repair and need to be recycled.
Repair and Refurbishing: Devices that can be repaired undergo a refurbishing process. Defective components are replaced, software is updated, and cosmetic imperfections are addressed. These refurbished devices are then restored to a like-new condition.
Recycling: Smartphones that are irreparable or outdated are directed toward recycling. The company partners with specialized electronics recycling facilities to extract valuable materials like precious metals, plastics, and other components.
Material Recovery: Within the recycling facility, smartphones undergo disassembly, with their constituent parts meticulously separated. Precious materials like gold, silver, copper, and plastics are retrieved to be repurposed in the production of fresh electronic goods.
Proper Disposal: Any hazardous materials or components that cannot be recycled are properly disposed of according to environmental regulations to minimize their impact on the environment.
Reuse and Resale: After refurbishing, the smartphones that have been repaired are tested and verified to be in working condition. They are then reintroduced into the market as certified refurbished devices, providing customers with cost-effective alternatives to new smartphones.
By implementing reverse logistics in this manner, the electronics company achieves several benefits:
Environmental Responsibility: The company minimizes electronic waste by recycling and reusing components, reducing the strain on natural resources.
Customer Satisfaction: Efficient returns and repairs enhance customer satisfaction by resolving issues promptly and providing refurbished devices as alternatives.
Cost Savings: The company recaptures value from returned devices through refurbishing and resale, contributing to revenue generation and reducing waste disposal costs.
Sustainability: The process aligns with the principles of a circular economy by extending the lifecycle of products and materials.
Leverage FarEye to optimize your reverse logistics
FarEye is a reverse logistics technology platform that offers solutions for optimizing various aspects of supply chain and logistics operations, including reverse logistics. FarEye provides tools and features that help companies streamline and enhance their reverse logistics processes. Here's how FarEye can help optimize reverse logistics for companies:
Visibility and Tracking: FarEye offers real-time visibility into the entire reverse logistics journey, from product returns to final disposition. This helps companies track the movement of returned items, assess their condition, and make informed decisions about the next steps.
Efficient Workflows: The platform enables companies to create efficient workflows for handling returned products. FarEye's automation capabilities help reduce manual tasks, ensure consistent processes, and eliminate bottlenecks in the reverse logistics chain.
Disposition Decision: FarEye provides data-driven insights to assist companies in making disposition decisions. By analyzing factors such as product condition, historical data, and demand patterns, businesses can decide whether to refurbish, resell, recycle, or dispose of returned items.
Route Optimization: For returns that require physical transportation, FarEye's route optimization capabilities help plan the most efficient routes, minimizing transportation costs and delivery times.
Communication with Customers: FarEye enables companies to keep customers informed about the status of their returns through automated notifications and tracking updates. This improves customer satisfaction and reduces inquiries.
Repair and Refurbishing Management: The platform helps manage the repair and refurbishing processes by assigning tasks, tracking progress, and ensuring quality control. This is especially useful for companies that refurbish returned items for resale.
Recycling and Disposal Compliance: FarEye assists in ensuring that returned items are processed in compliance with recycling and disposal regulations. This helps companies avoid legal issues and environmental violations.
Data Analysis and Reporting: Through its analytical and reporting functionalities, FarEye furnishes insights into the performance of reverse logistics, enabling companies to pinpoint potential areas for enhancement, gauge KPIs, and make decisions informed by data.
Collaboration: The platform facilitates collaboration among various stakeholders involved in reverse logistics, including customers, retailers, repair centers, recycling partners, and transportation providers.
Customization: FarEye's offerings can be customized to align with the distinct requirements of diverse industries and organizations. This ensures that the platform can adapt to the unique challenges and processes of each organization's reverse logistics operations.
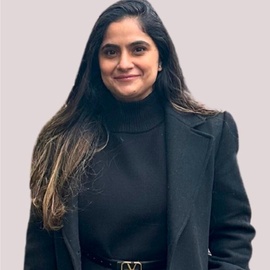
Komal Puri is a seasoned professional in the logistics and supply chain industry. As the AVP of Marketing and a subject matter expert at FarEye, she has been instrumental in shaping the industry narrative for the past decade. Her expertise and insights have earned her numerous awards and recognition. Komal’s writings reflect her deep understanding of the industry, offering valuable insights and thought leadership.
Let's Talk to Our Experts and Optimize Your Deliveries Today!
An expert from our team will reach out within 24 hours