- Logistics
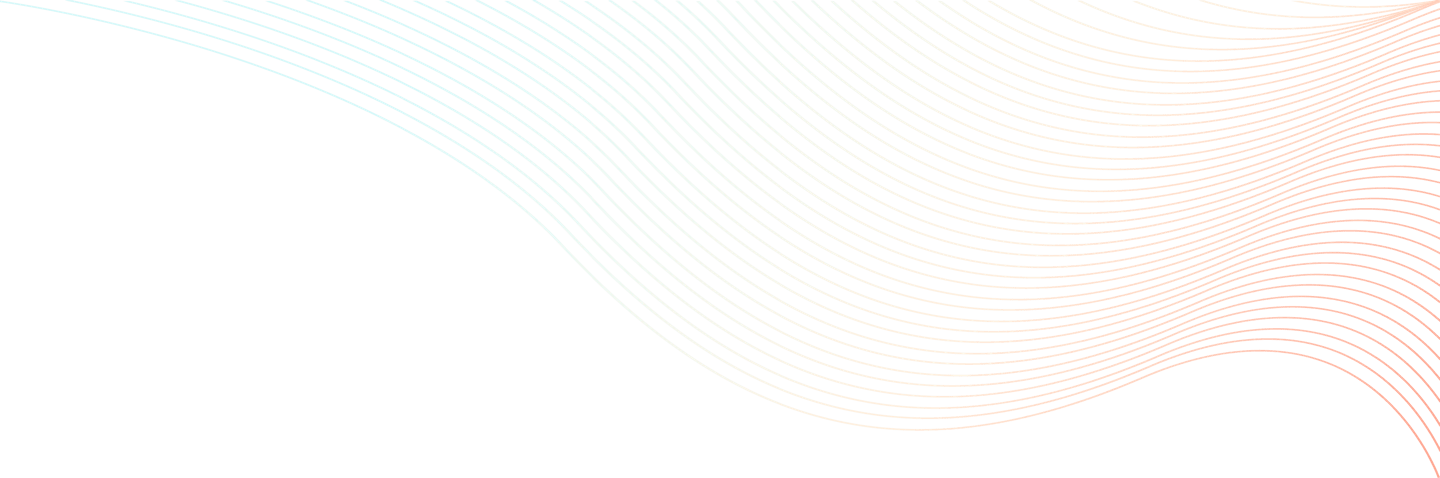
How Modern Warehouse Logistics Improves Delivery Speed and Inventory Accuracy
48% of customers today expect same-day deliveries, thanks to quick commerce and the demand for instant gratification.Yet many of these deliveries fall short of expectations, often due to bottlenecks that begin inside the warehouse. When order volume surges at 2 PM and trucks leave by 6, even a short delay in packing or staging can break the SLA. In today’s fulfillment cycle, every hour between order and dispatch matters.
Warehouse logistics plays a critical role in keeping that cycle on track. It connects inventory, labor, and outbound processes in real time turning visibility into action before problems surface.
Speed without accuracy creates waste, and accuracy without speed creates penalties. Warehouse logistics brings both into sync, supporting scale without sacrificing control.
This article breaks down how warehouse logistics drives delivery speed and inventory accuracy at enterprise scale.
What Is Warehouse Logistics?
Warehouse logistics is the management of the physical flow and digital tracking of goods from receiving to final dispatch. It ensures smooth movement, accuracy, and coordination throughout storage, picking, packing, and outbound scheduling.
The Flow of Data in Warehouse Logistics
Warehouse logistics depends on how well systems speak across every action. Here’s how real-time data flow supports every warehouse move:
- Inbound Visibility & Sync: Goods are scanned at the dock and matched with ASN records. Put-away starts immediately without manual verification delays.
- Live Stock Updates: Any inventory movement, such as picking, relocation, or return, triggers an instant update in system stock levels.
- System Integration: WMS, OMS, and TMS reflect the same order and inventory status. Teams don’t need to cross-check between platforms.
- Load Validation: Packed orders are checked using weight or dimension scans. Orders that don’t match are flagged before dispatch.
- Unified Data Layer: All warehouse activities connect to a central system. This allows both upstream and downstream teams to see the same record of events.
All of this needs an orchestration layer that comes with platforms like FarEye. Once an order is validated and ready to leave the dock, FarEye syncs that data with carrier systems, delivery schedules, and customer updates. It ensures that outbound visibility doesn’t stop at the warehouse door but extends through the entire last-mile experience.
How Warehouse Logistics Affects Inventory Accuracy?
Inventory accuracy depends on process structure and timing. Here’s how logistics controls the way stock data is captured and trusted:
- Layout and Slotting Discipline: Unstructured layouts lead to incorrect picks and delays. Logistics-driven slotting creates predictable paths and minimizes misplacement risks.
- Workflow Timing and Data Sync: When movements aren’t logged in real time, stock data deviates. Timed workflows reduce lags and keep systems in sync.
- Put-Away and Picking Process Design: Randomized or ad-hoc decisions delay operations. Logistics assigns logic to each move, keeping picks clean and repeatable.
- Task Ownership and Accountability: Overlapping responsibilities often cause stock gaps. Warehouse roles must be defined so that each transaction has a clear owner.
- Return Routing and Adjustments: Returns often bypass core workflows and inflate errors. Logistics frameworks must embed them into daily movement plans.
What is the Difference Between Inbound and Outbound Logistics Flow
Inbound logistics brings goods into the warehouse, while outbound logistics handles what goes out. One manages supply, and the other manages delivery.
Here’s a quick comparison of the key differences:
Attribute | Inbound Logistics | Outbound Logistics |
Direction | Inward movement from suppliers to warehouse | Outward movement from warehouse to customer |
Focus | Supply, stocking raw materials and replenishment goods | Demand, fulfilling customer orders |
Role | Receiving, inspecting, and storing goods | Picking, packing, staging, and shipping orders |
Key Relationships | Suppliers, vendors, and upstream distributors | Retailers, carriers, and end customers |
Core Processes | Sourcing, unloading, quality check, put-away | Order picking, packing, labeling, dispatch, returns |
Data Capture | ASN, GRNs, inspection records | Order slips, shipping labels, proof of delivery |
Systems Involved | ERP, supplier portals, warehouse receiving modules | WMS, OMS, TMS |
Activity Type | Incoming stock or materials for future processing | Outgoing finished goods for customer delivery |
Strategic Imperative | Securing the inputs needed to operate or manufacture | Meeting service levels and supporting revenue commitments |
How to Handle Inventory Effectively in Warehouse Logistics
For logistics leaders,tight control from inbound receipt to outbound dispatch preserves capital, protects delivery promises, and frees space for growth.
Below are eight actions that secure a reliable inventory flow:
Align Inbound Flow with Demand
Schedule carrier arrivals based on real-time needs. Use scan-based receiving and cross-docking to minimize dwell time.
Design Space for Frictionless Movement
Set up straight aisles and place fast movers near packing zones for quicker access.
Strengthen the Putaway Process
Follow system-driven rules and update inventory visibility immediately after putaway.
Execute Smarter Stock Takes
Use mobile scanning and rolling counts to check stock without disrupting operations.
Prioritize Accurate Cycle Counting
Count high-value or fast-moving SKUs more often and fix repeat errors using system alerts.
Track Lots and Serial Numbers Proactively
Scan lot and serial numbers early and link them to orders for traceability and compliance.
Refine Outbound Order Planning
Use real-time inventory and dock data to schedule dispatches more efficiently.
FarEye integrates with warehouse systems here to coordinate outbound flow based on order readiness, dock availability, and delivery timelines.
Perfect the Process
The right use of last-mile tools can greatly help reduce delivery errors.
It’s important to note that effective warehouse logistics starts with inventory control but ends with delivery precision. Once an order is picked, packed, and ready to go, the baton passes from WMS to last-mile delivery solutions.
FarEye bridges this gap by translating warehouse readiness into delivery precision, automating dispatch decisions, optimizing routes, and enforcing SLAs in real time.
When last-mile coordination is aligned with warehouse execution, fulfillment becomes faster, more predictable, and more cost-efficient.
Factors that Impact Warehouse Logistics
Even well-equipped warehouses face challenges when visibility, coordination, or control breaks down. Such problems affect fulfillment speed, accuracy, and the cost for each order.
Here are five factors that disrupt warehouse logistics:
Manual Inventory Updates
Without automated sync, stock data gets outdated. It leads to mis-picks and delays in replenishment. Often, it results in orders being filled with the wrong or unavailable items.
Fragmented Inbound and Outbound Visibility
When receiving and shipping data don’t align, teams can't manage dock usage or staffing efficiently. It leads to idle labor, missed staging windows, and late dispatches.
Poor System Integration
A disconnected tech stack slows execution. Without seamless data handoffs between WMS, OMS, and TMS, teams fall back on manual fixes, causing missed scans and broken order flow.
Static Slotting and Picking Logic
Fixed slotting ignores seasonality and SKU velocity. It increases walk time, lowers pick rates, and ultimately delays delivery, especially during high-volume periods.
No Reverse Logistics Framework
Returned items often go unprocessed without clear workflows. As they sit uncounted, available inventory appears lower than it is, triggering unnecessary reorders or stock gaps.
Key Capabilities of a Modern Warehouse Logistics System
Modern warehouse logistics depends on system intelligence, not operator guesswork. The right capabilities can compress cycle times and correct fulfillment errors before they occur.
Here are 5 key capabilities of modern warehouse logistics:
- Real-Time Inventory Visibility: From inbound dock to outbound gate, you need to know where each item sits. Tracking across bins and zones must update in real time. That prevents stockouts, avoids over-ordering, and reduces delays across fulfillment.
- Smart Inbound and Outbound Orchestration: Idle docks create backlogs and missed windows ripple downstream. A connected system dynamically matches shipments with available doors to reduce delays and keep flows predictable.
- Intelligent Slotting and Picking Logic: Static layouts slow high-velocity SKUs. Modern logic adapts to order priority and zone congestion, cutting travel paths and improving pick rate.
- End-to-End System Integration: Disconnected systems stall execution. Full integration across OMS, WMS, TMS, and ERP lets data move as fast as the product.
- Reverse Logistics Automation: Returns pile up without structure. A smart warehouse logs each return in real time, restocks it fast, and closes the loop without adding labor overhead.
Must-Have Warehouse Logistics Tech Stack to Enable Execution
Selecting the right technology stack turns warehouse logistics from reactive to predictive. Leaders need tools that allocate labor, surface live data, and adapt to volume spikes without costly head-count increases.
Below are three essential tech components for execution:
Warehouse Management System (WMS)
A warehouse management system is the command layer for warehouse logistics. It assigns tasks in real time, guides pickers along paths, and updates inventory the moment a scan posts. With decisions made inside the system, performance stays consistent even when order volumes double
Automation Infrastructure
Automation technologies enhance operational efficiency. Autonomous robots move totes between areas while pick-to-light guides workers to the correct SKU. RFID portals confirm each load as it leaves, which reduces manual checks and allows supervisors to focus on managing exceptions.
Visibility Platforms
Data loses value if people cannot see it when decisions are made. A visibility platform like FarEye stitches inbound, storage, and outbound signals into a single view that refreshes every few seconds. Planners watch dock clocks, inventory heat maps, and carrier ETAs on one dashboard, steering resources before delays form.
Why FarEye Powers Agile, Accurate Warehouse Logistics
Warehouse execution depends on speed and control and FarEye gives businesses exactly that. FarEye’s platform connects warehouse teams to the entire supply chain, providing centralized visibility and predictive alerts so you can act before delays or disruptions affect customers.
Below are five FarEye capabilities that deliver measurable gains:
Centralized Control Across Multi-Warehouse Networks
FarEye’s control tower presents inbound queues, live pick status, and outbound ETAs on one screen. This centralized view helps teams spot issues early and keep everything on track.
Read how our Southeast-Asian cold-chain provider achieved 100% real-time visibility after deployment.
Predictive Exception Management
AI flags potential order or slot delays before they break SLAs, letting teams reroute shipments proactively. The largest healthcare distributor in Asia-Pacific boosted vehicle capacity by 30% using these insights.
Seamless Integration with Core Systems
FarEye quickly connects with WMS, TMS, OMS, and ERP platforms, enabling zero-code onboarding. UK marketplace Creoate cut partner integration time by 90%.
Configurable Workflows for Every Site
Role-based builders let managers adjust scan points, quality gates, or dock rules without IT tickets. This flexibility keeps regional warehouses compliant with local labor policies while protecting global KPIs.
Built for Automation Compatibility
FarEye streams task updates to AMRs, pick-to-light arrays, RFID portals, and IoT sensors, enabling seamless automation and real-time accuracy across warehouse operations.
Looking to modernize warehouse operations for speed and precision? Request a demo with FarEye’s enterprise logistics experts.
Execution Speed and Inventory Confidence Start with Connected Warehouse Logistics
Missed delivery windows and stockouts often stem from gaps between warehouse operations and last-mile delivery. When receiving, slotting, and picking are aligned with real-time delivery needs, speed and accuracy improve across the entire supply chain.
FarEye bridges this gap by connecting warehouse workflows with last-mile execution, detecting delays before they impact SLAs, and delivering real-time updates to all teams and systems involved. This integration ensures faster throughput, fewer errors, and full visibility from warehouse to customer doorstep.
See FarEye in action. Book your personalized warehouse logistics demo today.
Frequently Asked Questions
How Does Warehouse Logistics Impact Last-Mile Delivery?
Warehouse logistics affects last-mile delivery by determining the speed and accuracy of order picking, packing, and shipping. Delays at this stage reduce the available delivery windows. An efficient warehouse ensures orders are sent out on time, which improves SLA performance and delivery reliability in various areas.
What KPIs Improve After Digitizing Warehouse Workflows?
Digitizing warehouse workflows helps improve performance metrics across inbound, storage, and dispatch. Commonly impacted KPIs include:
- Order picking accuracy
- Inventory turnover rate
- On-time dispatch percentage
- Dock-to-stock cycle time
- Labor productivity
Does FarEye Support Automation Tools Like AMRs and RFID?
Yes, FarEye integrates with automation tools such as AMRs, RFID scanners, and IoT sensors. It streams real-time task updates across systems. And it also helps warehouses coordinate faster movement, accurate tracking, and better exception handling.
How Quickly Can FarEye Be Deployed Across Multiple Warehouse Sites?
FarEye offers rapid deployment with minimal IT involvement. Its pre-built connectors and configurable workflows allow companies to launch across warehouse sites in just a few weeks.
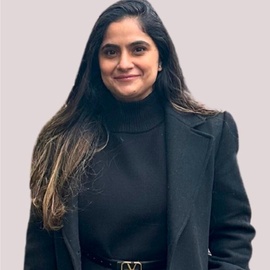
Komal Puri is a seasoned professional in the logistics and supply chain industry. As the AVP of Marketing and a subject matter expert at FarEye, she has been instrumental in shaping the industry narrative for the past decade. Her expertise and insights have earned her numerous awards and recognition. Komal’s writings reflect her deep understanding of the industry, offering valuable insights and thought leadership.
Let's Talk to Our Experts and Optimize Your Deliveries Today!
An expert from our team will reach out within 24 hours