- Logistics
- Logistics Complexity
- Track
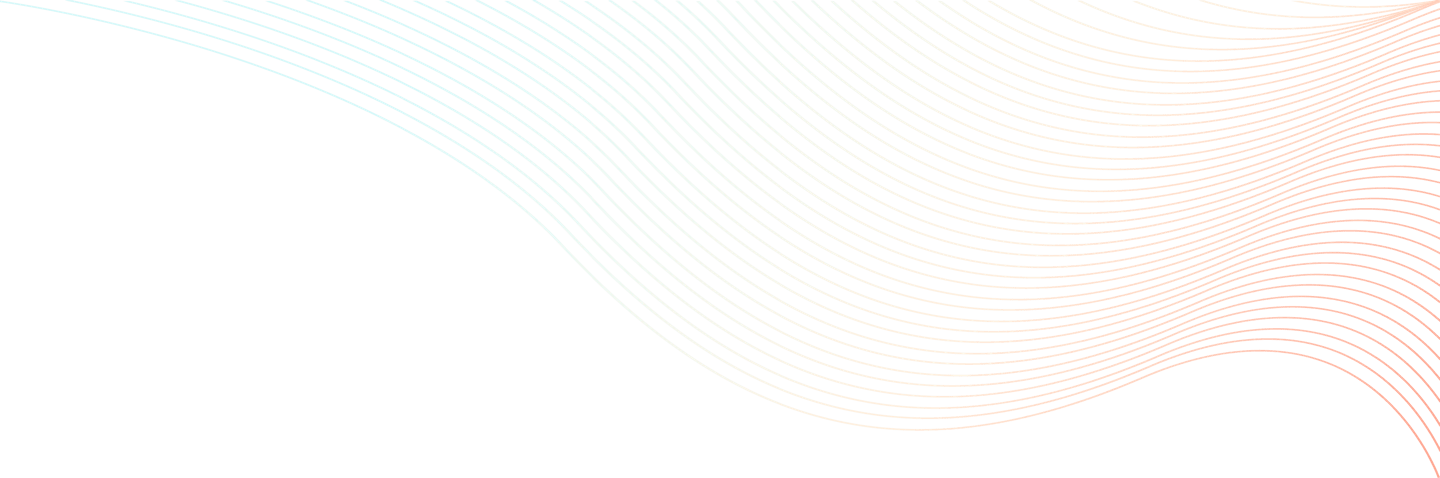
What is a Carrier Facility? The Ultimate Guide to Carrier Facilities & Tracking
Carrier facility plays a pivotal role in the seamless movement of goods and services within the supply chain. Serving as a central hub, these facilities serve as the nexus for transportation, warehousing, and distribution operations.
Carrier facilities act as critical links in the logistics network, ensuring timely delivery, minimizing transit times, and enhancing operational efficiency. Their integration with advanced technologies and strategic location makes carrier facilities indispensable components of the logistics ecosystem.
What is a carrier facility?
A carrier facility is a large warehouse or distribution center managed by shipping companies like UPS, FedEx, USPS etc. where packages and couriers are sorted, processed, and dispatched to their final destinations. These facilities act as a hub in the shipping network.
Types of Carrier Facilities in Ecommerce
A. Warehouses and Fulfillment Centers
1) Overview of Warehouses and Fulfillment Centers in Ecommerce:
Warehouses and fulfillment centers are key components of the ecommerce supply chain. Warehouses are storage facilities where inventory is stored, while fulfillment centers handle order processing and shipment preparation. These facilities play a crucial role in ensuring timely and accurate order fulfillment for online retailers.
2) Functions and Operations within Warehouses and Fulfillment Centers:
Within warehouses and fulfillment centers, various functions and operations take place. These include receiving incoming inventory, organizing and storing products, picking items from shelves to fulfill orders, packing orders, and preparing them for shipment. These facilities often employ technologies like barcode scanning, automated storage and retrieval systems (AS/RS), and conveyor systems to enhance efficiency.
3) Role of Warehouses and Fulfillment Centers in Order Processing and Inventory Management:
Warehouses and fulfillment centers contribute to streamlined order processing and effective inventory management. They ensure that products are readily available, maintain accurate stock levels, and optimize the allocation and fulfillment of orders. These facilities also play a crucial role in managing returns, inspecting products, and restocking inventory.
B. Distribution Centers and Sorting Facilities
1) What are Distribution Centers and Sorting Facilities?
Distribution centers are strategically located facilities that act as intermediate points in the supply chain, receiving inventory from warehouses and fulfilling bulk shipments to regional locations or retail stores. Sorting facilities are specialized centers that handle the sorting and consolidation of shipments based on their destinations.
2) Importance of Distribution Centers for Efficient Order Fulfillment:
Distribution centers play a crucial role in efficient order fulfillment by enabling faster and cost-effective delivery to customers. By strategically positioning distribution centers closer to end-customers, ecommerce businesses can reduce transit times and shipping costs, improving customer satisfaction.
3) Sorting Technologies and Processes in Distribution Centers:
Sorting facilities employ various technologies and processes to streamline the sorting and consolidation of shipments. This includes automated sorting systems, conveyor belts, barcode scanning, and label printing. These technologies enhance accuracy and efficiency, enabling faster processing and routing of shipments to their respective destinations.
C. Last-Mile Delivery Hubs and Pickup Points
1) Understanding Last-Mile Delivery Hubs and Pickup Points:
Last-mile delivery hubs are locations where shipments are consolidated for final delivery to individual customers. They act as distribution points within specific geographic areas. Pickup points, on the other hand, are designated locations where customers can collect their orders, providing an alternative delivery option.
2) Optimization Strategies for Last-Mile Delivery in Ecommerce:
Last-mile delivery is a critical and challenging aspect of ecommerce logistics. Optimization strategies include route planning and optimization, dynamic dispatching, and real-time tracking to ensure efficient and timely deliveries. Utilizing technology solutions, such as route optimization software and GPS tracking, helps optimize delivery routes and schedules.
3) Role of Pickup Points in Enhancing Customer Convenience:
Pickup points offer convenience to customers who may prefer to collect their orders at a location of their choice, such as a nearby retail store or locker. They provide flexibility, eliminate the need for home delivery, and reduce the chances of missed deliveries. Pickup points can improve overall customer experience by offering convenience and flexibility in receiving their ecommerce orders.
What are the 4 biggest carrier facilities?
1) Amazon Fulfillment Centers:
Amazon's fulfillment centers are massive carrier facilities designed to handle the warehousing, order processing, and fulfillment needs of the company. These centers are strategically located around the world to ensure quick and efficient delivery to customers. They are equipped with advanced technologies, such as robots and conveyor systems, to optimize inventory management, order picking, and packing processes. Amazon's fulfillment centers are known for their fast order processing capabilities, vast storage capacity, and sophisticated logistics operations.
2) United States Postal Service (USPS):
As a government-operated postal service, USPS operates a vast network of carrier facilities that include sorting centers, processing hubs, and local post offices. These facilities handle a wide range of mail and packages, serving as key distribution points within the USPS network. USPS carrier facilities are responsible for sorting and routing mail and packages, ensuring timely delivery across the United States. These facilities also provide additional services such as PO box rentals, retail services, and passport application processing.
3) FedEx Distribution Centers:
FedEx operates a network of distribution centers worldwide to facilitate its global logistics operations. These facilities play a crucial role in receiving, sorting, and distributing packages within the FedEx network. Distribution centers are strategically located near transportation hubs to ensure efficient transit and timely delivery. They employ advanced technologies, such as automated sorting systems and real-time tracking, to optimize package handling and tracking processes. FedEx distribution centers are essential for the company's reliable and speedy delivery services.
4) UPS (United Parcel Service) Facilities:
UPS operates a vast network of carrier facilities, including package sorting hubs, distribution centers, and local UPS stores. These facilities are integral to UPS's logistics infrastructure and support its delivery operations. Package sorting hubs act as central points for sorting and consolidating shipments, ensuring efficient routing for timely delivery. Distribution centers manage inventory and facilitate the movement of packages to local delivery hubs. Local UPS stores provide retail services and serve as access points for drop-off and pickup of packages. UPS facilities are known for their extensive coverage and reliable delivery services.
How FarEye Benefits Carrier Facilities
i) Enhanced Visibility and Tracking
- Real-time tracking of shipments and vehicles: Fareye provides real-time tracking capabilities that enable carrier facilities to monitor the movement and location of shipments and vehicles throughout the delivery process. This helps improve operational efficiency, reduce delays, and enhance customer satisfaction by providing accurate and up-to-date information about the status of deliveries.
- Route optimization and geofencing capabilities: Fareye's route optimization and geofencing features help carrier facilities optimize delivery routes based on factors such as traffic conditions, delivery priority, and vehicle capacity. Geofencing allows for setting up virtual boundaries and triggers alerts when a vehicle enters or exits a specific area. These capabilities enable carriers to plan and execute deliveries more efficiently, resulting in reduced fuel costs, shorter delivery times, and improved resource allocation.
- Improved visibility for customers and stakeholders: By leveraging Fareye, carrier facilities can provide enhanced visibility to customers and stakeholders. Fareye's tracking features allow customers to track their shipments in real-time, providing transparency and peace of mind. Additionally, Fareye's dashboard and reporting tools provide comprehensive insights and analytics to carrier facilities, enabling them to make data-driven decisions and improve overall operational performance.
ii) Efficient Dispatch and Routing
- Automated dispatching and allocation of tasks: Fareye's automated dispatching feature optimizes the allocation of delivery tasks based on factors such as proximity, capacity, and priority. This streamlines the dispatch process, reduces manual intervention, and ensures efficient utilization of resources within carrier facilities.
- Dynamic routing to optimize delivery schedules: Fareye's dynamic routing capabilities enable carrier facilities to optimize delivery schedules based on real-time traffic conditions, customer preferences, and other variables. This helps minimize delivery delays, optimize fuel consumption, and improve overall delivery efficiency.
- Minimization of empty miles and improved resource utilization: Fareye helps carrier facilities minimize empty miles by optimizing routes and load balancing. By maximizing the utilization of available resources, Fareye enables carrier facilities to handle more deliveries with fewer vehicles, reducing operational costs and environmental impact.
iii) Streamlined Proof of Delivery (POD) Process
- Digital POD capture with electronic signatures: Fareye enables carrier facilities to digitally capture proof of delivery using electronic signatures. Delivery personnel can use mobile devices or electronic signature pads to capture customer signatures, eliminating the need for paper-based documentation and reducing the chances of errors or loss of paperwork.
- Integration with barcode scanning and image capture: Fareye integrates with barcode scanning and image capture technologies, allowing carrier facilities to capture and associate important information, such as package barcodes or images, with the delivery process. This enhances accuracy, improves traceability, and provides additional evidence of delivery.
- Instant POD verification and retrieval for faster billing and customer service: With Fareye, carrier facilities can quickly verify and retrieve proof of delivery information for billing purposes and customer inquiries. This streamlines administrative processes, reduces paperwork, and enhances customer service by providing swift and accurate information about completed deliveries.
Overall, Fareye offers several benefits for carrier facilities, including enhanced visibility and tracking, efficient dispatch and routing, and streamlined proof of delivery processes.
By harnessing the cutting-edge capabilities provided by Fareye, carrier facilities have the opportunity to enhance their operations to a remarkable extent, resulting in amplified customer satisfaction and an overall elevation in operational excellence.
Fareye's advanced features empower carriers to streamline their processes, enabling them to efficiently allocate and utilize resources, optimize routing and scheduling, and enhance last-mile delivery operations. This not only enhances operational efficiency but also enables carriers to meet and exceed customer expectations by providing timely and accurate updates, real-time tracking, and improved delivery experiences.
By embracing Fareye's innovative solutions, carrier facilities can unlock the full potential of their operations and cultivate a reputation for excellence in the industry.
FAQ’s
a) What does "Package arrived at a carrier facility" mean?
When tracking information states that a package has arrived at a carrier facility, it indicates that the package has reached a specific location within the carrier's network, such as a sorting center, distribution center, or warehouse. This facility serves as a hub where packages are received, sorted, and prepared for further transportation to their destination. "Package arrived at a carrier facility" essentially means that the package has completed one stage of its journey and is now within the carrier's system for further processing and delivery.
b) What does "Package has left the carrier facility" mean?
When tracking information indicates that a package has left the carrier facility, it means that the package has been processed, sorted, and loaded onto a vehicle or transferred to another facility for onward transportation. This milestone suggests that the package has moved beyond the carrier facility and is now en route to its next destination, which could be another sorting center, a local distribution hub, or directly to the recipient's address. "Package has left the carrier facility" signifies that the package has moved closer to reaching its final destination.
c) Why is tracking your order important?
Tracking your order is important for several reasons:
a) Ensuring Shipment Visibility: Tracking enables you to have constant oversight of your package, starting from the moment it is dispatched until it arrives at your doorstep. It offers live updates regarding its location, estimated delivery dates, and potential delays.
b) Peace of Mind: Tracking provides peace of mind, as you can stay informed about the status of your package and have an estimated timeline for its arrival. This helps alleviate concerns about lost or delayed shipments.
c) Delivery Planning: By tracking your order, you can plan accordingly for the delivery. You can ensure that someone is available to receive the package or make arrangements for alternative delivery options if needed.
d) Issue Resolution: In case of any delivery issues or discrepancies, tracking information can be used as evidence to resolve problems with the carrier or retailer. It helps identify the location or stage where an issue occurred, aiding in efficient resolution.
e) Customer Satisfaction: Tracking your order is crucial for a positive customer experience. It provides transparency, builds trust, and allows you to communicate accurate delivery information to customers if you are a seller or retailer.
d) Can you pick up your package at a carrier facility?
In many cases, it is possible to pick up your package at a carrier facility, although this depends on the carrier's policies and the specific circumstances of the shipment. Some carriers offer a service called "Hold for Pickup" or "Will Call," which allows recipients to collect their packages directly from a carrier facility instead of having them delivered to their address. This option is particularly useful when a recipient prefers to avoid missed deliveries or wants to pick up the package at their convenience. However, it is important to check with the carrier and follow their guidelines and procedures for package pickups to ensure a smooth and hassle-free experience.
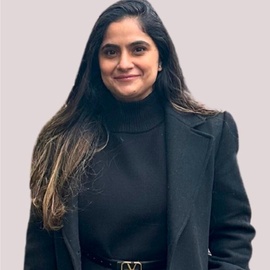
Komal Puri is a seasoned professional in the logistics and supply chain industry. As the AVP of Marketing and a subject matter expert at FarEye, she has been instrumental in shaping the industry narrative for the past decade. Her expertise and insights have earned her numerous awards and recognition. Komal’s writings reflect her deep understanding of the industry, offering valuable insights and thought leadership.
Let's Talk to Our Experts and Optimize Your Deliveries Today!
An expert from our team will reach out within 24 hours