- Logistics
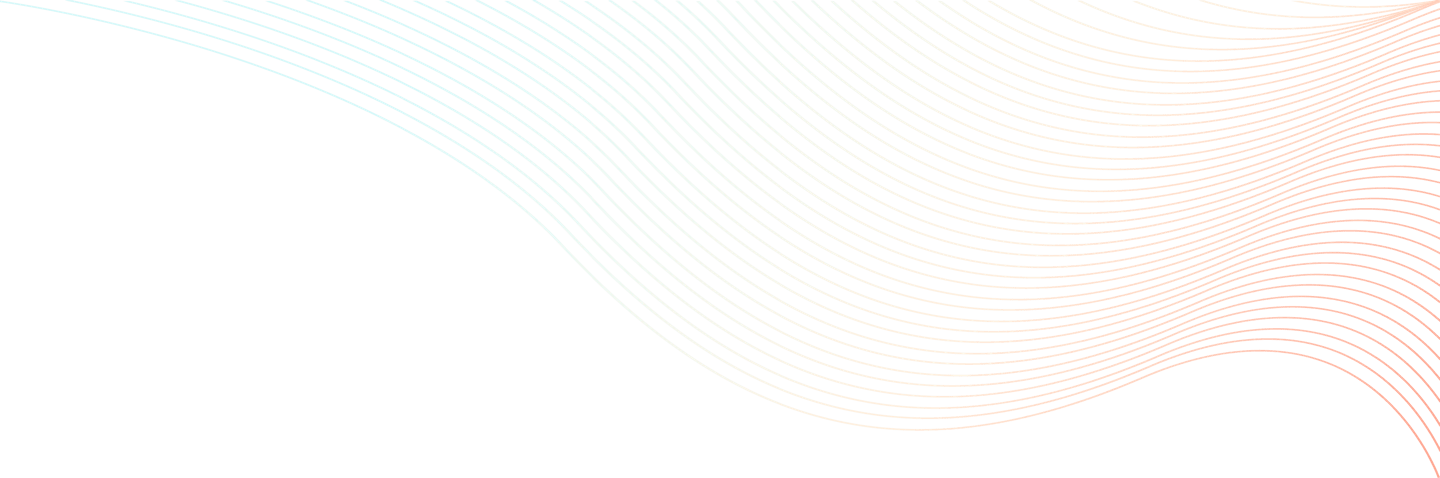
What is outbound logistics? How to optimize outbound logistics processes using cutting edge software
Optimizing outbound logistics management is of crucial significance in maintaining a well-oiled supply chain. Indications that your outbound logistic activities need tweaking include shipment errors, erroneous invoices, poor customer experience, delayed deliveries and insufficient inventory supplies. To refer to these errors as the “cost of doing business” is often erroneous. There are many factors that you’re more in control of than you may think. Profit loss and customer dissatisfaction resulting from these avoidable mistakes can be eliminated when the best outbound logistics system is implemented for your company’s needs.
According to Deloitte, 79% of companies with optimally functioning supply chains produced above-average revenue growth. Comparatively, only 8% of companies running with slower and less efficient supply chains experienced a significant increase in profit. The impact of a highly effective outbound logistics system should not be underestimated.
What is outbound logistics?
The term outbound logistics encompasses activities from the production or collection of goods all the way through to delivering them to the customer. It includes monitoring production, collecting required amounts of inventory, picking and packing orders according to accurately generated and processed invoices, and managing a flow through various delivery options. Running these outbound logistics activities effectively are of crucial importance to your organization’s success.
Outbound logistics and inbound logistics work together but maintain differing roles. Inbound logistics processes include the movement of raw materials, finished goods, and supplies from a manufacturer or other distribution channel to a warehouse or retail store. Outbound logistics processes relate to processing and transporting products to the consumer. Outbound logistics processes typically begin in a distribution centre and end when the order reaches the final destination.
Choosing the right outbound logistics system according to your organization’s needs will automate the process with fewer errors and more accurately access the factors influencing outcomes. Outbound logistics systems also help redirect potential errors and allow the user to navigate back to see how to fix mistakes. These systems will guide faster and more accurate deliveries as they route the orders into trailers. Logs will be produced, and may data may be compiled and accessed for future reference electronically.
How Outbound Logistics Impacts Distribution of Finished Goods and Products
Outbound logistics activities influence how products are distributed from the place of manufacture to the customer’s destination. Delays in delivery are among prominent potential insufficiencies in the outbound logistics system. They are linked to unnecessary expenses for the buyer and supplier which could be otherwise avoided when the shipping time is calculated properly.
Manufacturing deadlines fail to be met also when raw materials are not readily available. When your business fails to deliver on time, buyers often look to your competitors as alternative suppliers. Clients are lost and overall profitability is hindered. Additionally, if the product being shipped is perishable, its value declines or is altogether lost when they are delivered late.
Success in your outbound logistics in supply chain management may also be impacted by theft. External threats to security include hijacked shipments or being targeted by hackers online, while internal threats could come from employees with an intent to steal from the company. An outbound logistics example of theft may also be sabotaging shipments.
Inaccurate route planning could lead your shipments into congestion points in traffic and waste valuable time, impairing productivity and increasing profit loss. It may also inadvertently put drivers at personal risk by pressuring them to drive faster and/or on less sleep. You may also blow your payroll budget due to paying out for overtime or to meet the need to recruit, train, and hire additional drivers. Fuel is also used in excess when routes are planned poorly.
A well-selected outbound logistics system provides advanced visibility and a broader overview of shipments distribution. It aids your company’s ability to carry out satisfactory customer service by providing them with real-time updates. The relationship between inbound and outbound logistics can also be coordinated with the aim of conserving resources and labor.
Key Outbound Logistics Activities and Processes
It is important to take note of each of the many points relating to outbound logistics in supply chain management as small errors can equal big losses over time. If any of them are mismanaged, it may impact your company’s reputation negatively as well as cutting into profits.
Entering order information accurately will eliminate such problems as duplicate orders, shipping incorrect quantities, and accidentally sending the wrong product or using the wrong shipping address. Investing in outbound logistics management systems technology with enabled software will help guide the process in real-time. They also provide customers with the option of updating an order before they are loaded on trailers in the yard.
Delivery timelines are outlined by the availability of data related to inventory on hand and needs to be readily accessible to employees in outbound logistics management. Replenishing supply quantities need to be adequately addressed not only for immediate order fulfillment but also optimized for future available sales. Applying manual procedures in the picking and packing process is subject to error due to the complexity that arises from many steps in the process. The proper application of an outbound logistics system is required.
The logistics activities executed prior to and including picking and packing are part of replenishment operations, the process of preparing for future deliveries. These include label-based picking, paper-based picking, line picking, cluster picking, zone picking.
Theoretically functional outbound logistics activities streamline replenishment’s role in the supply chain and minimize manual labour.
Within the various outbound logistics processes, packing could be considered the most important in the sense that it contains complex variables whose outcome directly corresponds to accuracy in execution. These important steps in processing customer orders include packaging, labeling, inspecting and routing. If any of these are not completed adequately, shipping times are delayed or not delivered at all and customer relations are compromised.
Distribution Channels in Outbound Logistics
There are three main types of distribution channels in outbound logistics that involve a combination of four elements: product producer, wholesaler, retailer, and consumer. One type involves all four. This is sometimes chosen due to the nature or restrictions placed on selling the product. For example, if your company deals in alcoholic products, the laws in your state may require that they be sold to a wholesaler; a retailer cannot be dealt with directly.
The next channel uses only one intermediary, eliminating the wholesaler. The product is sold directly to the retailer who, in turn, sells to the end consumer. This type is typically used by larger well-known companies whose products are sold to retail giants.
The third channel extends directly from the product producer and the consumer. It is often referred to as a direct-to-consumer model. It doesn’t use a wholesaler or retailer at all. Apple is an example of a company that uses this model. They carry this out by maintaining the presence of flagship stores in malls. Many companies using e-commerce also employ this channel by selling products to consumers directly through their websites.
The main factors in choosing a distribution channel may include cost, speed, quality control, considering logistics complexity, and customer satisfaction.
4 Ways Outbound Logistics Processes Impact Customer Experience
1. Flawless deliveries
Maintaining address accuracy, delivering the package, ensuring the delivered products are in good condition, and maintaining transparency with the consumer are all fundamental in delivering a good final outcome in the outbound logistics process. This requires attention to detail in entering each order without error. Small mistakes can extend the time of delivery to the consumer resulting in bad reviews and promoting a poor reputation for your company.
2. On-time deliveries
On-time delivery managed by an outbound logistics system generates real-time updates to the customer. When a customer, for example, is provided with a notification that a shipment may be arriving later than expected, it mitigates the consumer’s disappointment when the delivery is late. Promoting transparency with the consumer helps boost consumer confidence that the company is in control of the narrative.
3. Data-driven processes
With quality data collection throughout the entire outbound logistics process, organizations and their partners can streamline operations. To gain this type of value, data sharing and collaboration are critical. Advanced visibility provides the opportunity for all parties to obtain information in real-time.
4. Increased visibility
A smartly executed outbound logistics process involves planning strategies related to technology and is the only means to gain visibility over the many factors influencing the supply chain, including varied geographical locations. The carrier locations cannot be tracked accurately and quickly through manual processes. Poor quality of data deprives you of predictive analytics capability, Advanced visibility is crucial for effective warehouse and transportation management.
How A Modern Outbound Logistics System Can Optimize Distribution Processes
The logistics industry has outgrown traditional processes used prior to the development of current technology. Advances in logistics variables have contributed to a greater range of complexities to manage. To accomplish this successfully, both human effort and modern technology need to be applied to a robust outbound logistics system.
Optimal route planning involves navigating many points along sometimes wide distances. Without the assistance of real-time tracking technology deliveries would be delayed, mismanaged, and productivity and profit loss would occur. Modern capabilities automate the itineraries of freight carrying vehicles and eliminate unnecessary stops and delays.
Outbound logistics management systems that are well run customize their suggestions according to the specific needs of your type of business. They are capable of generating data that networks your company with logistic departments moving similar types of inventory that may also be moving through similar geographical locations.
Predictive intelligence capabilities compile and compare data from past logs to produce optimal suggestions for future decisions in the outbound management processes. These contribute to an improved customer experience. The stakes are high to risk your investments otherwise. The entire production process that has led up to the delivery of goods is mismanaged and trickles down negatively to all aspects of your logistics business.
At a quick glance, outbound logistic functions appear to be straightforward, aiming to meet the simple goal of getting packages from one point to another. The complex processes involving paperwork, verification, and auditing prior to transit need to be comprehensively addressed. When outbound logistics systems are applied, these procedures are automated. When routine activities are covered, your resources can be redirected to other priorities.
Outbound logistics management platforms enable manufacturers to keep up the pace with the ability to manage multi-faceted and rapidly evolving variables of the industry. These are the required tools to address unnecessary costs, intervene to prevent transportation risks, and keep customers satisfied. Gaining real-time visibility of end-to-end delivery operations is an unparalleled asset to assist overall logistics operations. To manage increases in production demand without a modern outbound logistics system is nearly impossible and won’t be sustainable at all in the future. Taking the steps to update your outbound logistics system now will have an immediate impact as you find many of the pitfalls you previously experienced are now avoided.
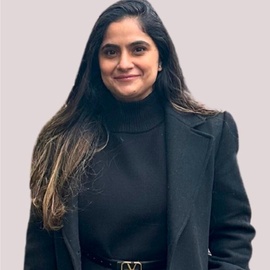
Komal Puri is a seasoned professional in the logistics and supply chain industry. As the AVP of Marketing and a subject matter expert at FarEye, she has been instrumental in shaping the industry narrative for the past decade. Her expertise and insights have earned her numerous awards and recognition. Komal’s writings reflect her deep understanding of the industry, offering valuable insights and thought leadership.
Let's Talk to Our Experts and Optimize Your Deliveries Today!
An expert from our team will reach out within 24 hours
Related resources
