- Last-Mile
- Delivery Scheduling
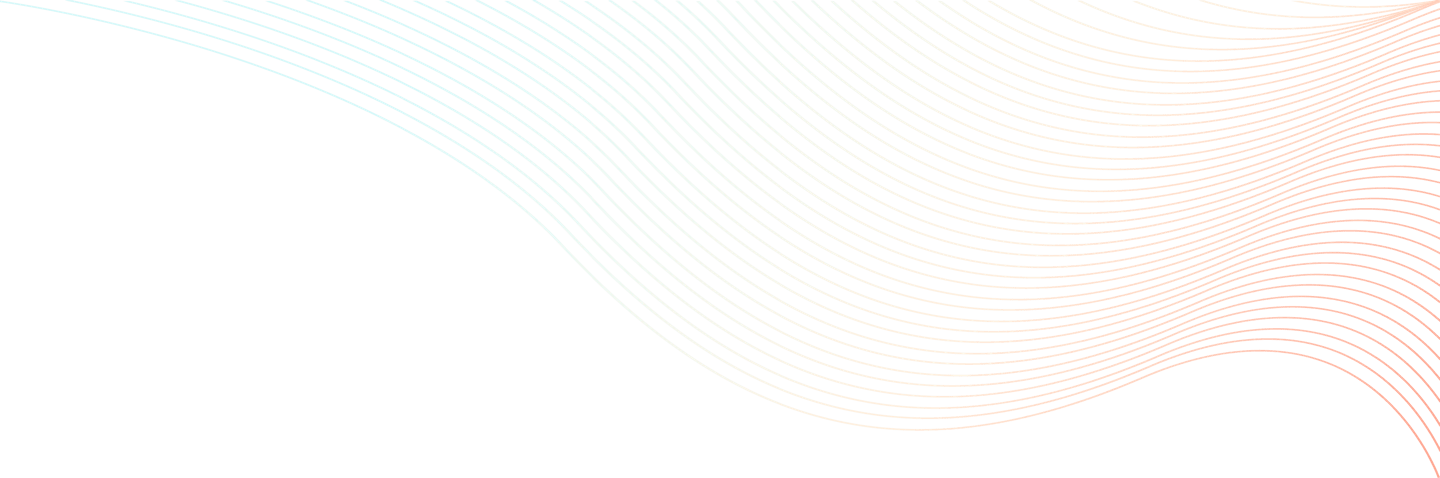
Key Performance Indicators (KPIs) in Logistics
What is a Logistics KPI?
A Logistics Key Performance Indicator (KPI) serves as a quantitative instrument adopted by businesses to assess the effectiveness of their logistics department. These KPIs encompass a wide range of metrics that touch upon areas such as procurement, warehousing, transportation, goods delivery, and financial aspects. These metrics provide valuable insights that help logistics managers make informed decisions and optimize their supply chain operations.
Importance of Monitoring KPIs for Logistics Managers
Monitoring Key Performance Indicators (KPIs) is of paramount importance for logistics managers as it serves as the compass guiding their departments toward efficiency, cost-effectiveness, and ultimately, success. In the complex world of logistics, where every minute and every resource counts, KPIs provide invaluable insights into various aspects of the operation. They help logistics managers track, analyze, and optimize crucial metrics related to purchasing, warehousing, transportation, delivery, and financials.
For logistics managers, the top priorities revolve around ensuring timely deliveries, maintaining product quality, and managing costs effectively. Lapses in any of these areas have the potential to exert a substantial influence on a company's financial performance. Through diligent monitoring of KPIs, logistics managers can promptly pinpoint bottlenecks, areas ripe for enhancement, and prospective avenues for reducing costs. Moreover, KPIs provide a data-driven basis for decision-making, allowing managers to make informed choices that enhance overall operational efficiency and customer satisfaction. In essence, monitoring KPIs empowers logistics managers to proactively address challenges, streamline processes, and drive their logistics departments toward achieving strategic goals. It goes beyond merely managing logistics; it's about optimizing performance and consistently delivering excellence with every shipment.
How to Create a Logistics KPI Program
- Identify Goals: Begin by defining your goals for the KPI program. What questions are you trying to answer? Examples include measuring delivery timeliness, labor availability, and transportation efficiency. Ensure your questions cover all aspects of your logistics operations.
- Set Achievable Targets: Establish achievable and reasonable targets for each KPI. Benchmarks can come from industry standards or historical data if available.
- Create a Dedicated Team: Form a team responsible for managing and analyzing the KPIs. These individuals should have expertise in the specific areas covered by the KPIs.
- Regularly Review and Act: Consistently review KPIs with the responsible team and take action based on the insights. Discuss the drivers behind each metric to understand the contributing factors.
How to Build Useful KPI Dashboards
Creating an effective KPI dashboard is essential to visualize and track logistics metrics efficiently. Here are some tips:
- Select SMART KPIs: Make certain your Key Performance Indicators are Specific, Measurable, Achievable, Relevant, and Time-bound. Avoid overly general or ambiguous metrics, and establish well-defined targets for each one.
- Avoid Information Overload: Don't overwhelm your team with too many KPIs. Begin with a manageable quantity and progressively expand as necessary. Remember that quality takes precedence over quantity.
- Hierarchical Structure: Organize your KPIs into two tiers of hierarchy—primary metrics for executives and more detailed metrics for middle managers and supervisors.
- Focus on Leading Indicators: Prioritize leading indicators that predict performance over lagging metrics that report on past performance. Staying ahead of potential issues is key.
- Clean Data is Crucial: Ensure your data is accurate and up-to-date. Multiple data sources and delays can lead to discrepancies. Consider using Business Intelligence (BI) software to consolidate and access real-time data.
Logistics KPI Examples
Now, let's explore logistics KPI examples across various categories:
Financial Logistics KPI Examples
1. Pick and Pack Costs
Role and Impact: Measures all costs related to picking and packing products, helping optimize processes and reduce expenses.
Significance: Effective handling of pick and pack expenses results in cost savings and enhanced profitability.
2. Operating Ratio
Role and Impact: Evaluates the relationship between operating expenses and revenue, indicating operational efficiency.
Significance: Maintaining a low operating ratio is crucial for financial sustainability and competitiveness.
3. Net Profit Ratio
Role and Impact: Assesses profitability relative to sales or total assets, providing insights into profit generation and asset management.
Significance: Understanding net profit ratios guides decisions on resource allocation and investment.
4. Inventory Turnover Ratio
Role and Impact: Evaluates the speed of product movement through the company, indicating demand and sales efficiency.
Significance: Higher inventory turnover reduces the risk of overstock and obsolescence.
5. Financial Leverage
Role and Impact: Measures the ratio of debts to assets, indicating financial risk and return on equity.
Significance: Balancing financial leverage is crucial for optimizing returns while managing debt risks.
6. Inventory to Sales Ratio
Role and Impact: Evaluates available inventory relative to actual sales, helping prevent overstock and supply chain disruptions.
Significance: Maintaining a balanced inventory-to-sales ratio ensures efficient inventory management.
Supply and Inventory Logistics KPI Examples
1. Capacity Utilization
Role and Impact: Measures resource use, optimizing production rates and reducing operating costs.
Significance: Efficient capacity utilization ensures sustainable goods flow and cost control.
2. Equipment Utilization Rate
Role and Impact: Tracks equipment use, indicating the need for additional equipment and preventing production delays.
Significance: Maintaining optimal equipment utilization ensures smooth operations.
3. Use of Packing Material
Role and Impact: Monitors packing material use, promoting cost savings and environmental responsibility.
Significance: Reducing packing material waste minimizes costs and environmental impact.
4. Pick and Pack Cycle Time
Role and Impact: Measures the time taken to pick and pack products, revealing process efficiency.
Significance: Setting reasonable cycle time targets boosts employee satisfaction and operational performance.
Transportation Logistics KPI Examples
1. Number of Shipments
Role and Impact: Monitors the volume of orders shipped, helping allocate resources effectively.
Significance: Insights into peak shipping hours enable better manpower planning and increased revenue.
2. Truck Turnaround Rate (Truck Turning) or Average Wait Time (Average Dwell Time)
Role and Impact: Measures the efficiency of loading and unloading processes, minimizing delays.
Significance: A quick turnaround and low wait times enhance overall shipping and receiving workflow.
3. Driver Performance
Role and Impact: Evaluates driver behavior through metrics like speed, idle time, and braking incidents.
Significance: Monitoring driver performance enhances safety, reduces maintenance costs, and ensures quality deliveries.
4. Fuel Efficiency
Role and Impact: Measures vehicle performance in terms of fuel consumption, impacting operating costs.
Significance: Improved fuel efficiency lowers operational expenses and increases competitiveness.
5. Compliance with Regulations
Role and Impact: Tracks adherence to transportation regulations and compliance standards.
Significance: Ensuring compliance reduces legal risks, fines, and disruptions in the supply chain.
6. Number of Shipments
Role and Impact: Monitors the volume of orders shipped, helping allocate resources effectively.
Significance: Insights into peak shipping hours enable better manpower planning and increased revenue.
7. Driver Performance
Role and Impact: Evaluates driver behavior through metrics like speed, idle time, and braking incidents.
Significance: Monitoring driver performance enhances safety, reduces maintenance costs, and ensures quality deliveries.
8. Fuel Efficiency
Role and Impact: Measures vehicle performance in terms of fuel consumption, impacting operating costs.
Significance: Improved fuel efficiency lowers operational expenses and increases competitiveness.
Delivery Logistics KPI Examples
1. Lead Time (Order Cycle Time)
Role and Impact: Measures the time from order placement to receipt, identifying bottlenecks and delays.
Significance: Reducing lead time enhances customer satisfaction and supply chain efficiency.
2. Delivery Time
Role and Impact: Tracks the duration from shipment to receipt by the customer, ensuring timely deliveries.
Significance: Reducing delivery time leads to more accurate delivery predictions and improved customer satisfaction.
3. Order Accuracy Rate
Role and Impact: Measures the rate of error-free orders, minimizing returns and revenue loss.
Significance: High order accuracy rates improve operational efficiency and customer trust.
Labor Logistics KPI Examples
1. Sick Leave
Role and Impact: Highlights employee health and safety, preventing disease spread and labor disruptions.
Significance: Promoting a healthy workforce enhances productivity and reduces absenteeism.
2. Safety (Number of Reportable Injuries, Accidents, or Fatalities)
Role and Impact: Enforces safety protocols, minimizing injuries, damages, and legal issues.
Significance: Prioritizing safety fosters a secure work environment and protects both people and assets.
3. Time to Fill Open Positions
Role and Impact: Gauges recruitment efficiency, reducing hiring process durations.
Significance: Faster hiring processes attract top talent and minimize workforce gaps.
How FarEye helps achieve the aforementioned KPIs in Logistics
In today's fast-paced world, the logistics industry is under immense pressure to deliver goods faster, more efficiently, and at a lower cost. To excel in this competitive landscape, logistics managers need more than just intuition; they need data-driven insights. This is where FarEye, a leading logistics and supply chain optimization platform, steps in to revolutionize how companies achieve their Key Performance Indicators (KPIs). Below, we'll explore how FarEye helps logistics managers meet and exceed their KPIs, leveraging the comprehensive set of metrics we discussed earlier.
On-Time Delivery:
FarEye's predictive analytics and route optimization algorithms empower logistics managers to ensure on-time deliveries. By analyzing historical data and real-time traffic information, FarEye helps in scheduling deliveries efficiently, minimizing delays, and meeting this critical KPI.
Product Quality & Handling:
Through real-time tracking and temperature monitoring, FarEye ensures that products are handled and transported with care. This not only helps maintain product quality but also reduces damage during transit, thereby positively impacting KPIs related to product quality.
Cost Control:
FarEye's optimization capabilities, including load balancing and fuel-efficient route planning, lead to reduced operational costs. This directly contributes to maintaining a low operating ratio and higher net profit ratio, two vital financial KPIs.
Inventory Management:
FarEye's demand forecasting and inventory optimization tools enhance inventory turnover ratios. Through careful stock management, logistics managers can prevent overstocking and stockouts, ensuring the right products are available at the correct time and location, ultimately contributing to a healthier bottom line.
Delivery Efficiency:
FarEye's dynamic route planning and real-time tracking reduce delivery times. This is reflected in improved delivery time and order accuracy rate KPIs, crucial for customer satisfaction and retention.
Resource Utilization:
FarEye helps logistics managers optimize resource utilization by providing insights into capacity and equipment utilization rates. This practice guarantees the allocation of the appropriate resources at the right time, effectively eliminating labor shortages and enhancing operational efficiency.
Safety and Compliance:
FarEye's driver performance monitoring tools promote safety by tracking metrics like speed, idle time, and hard-braking occurrences. This proactive approach aids in accident prevention and the maintenance of a secure work environment.
Environmental Considerations:
FarEye's emphasis on fuel efficiency not only cuts costs but also aligns with sustainability objectives. A higher fuel efficiency, as measured by logistics KPIs, translates to a reduced carbon footprint.
FarEye is more than just a logistics platform; it's a strategic ally for logistics managers striving to meet and exceed their KPIs. By leveraging advanced technologies such as predictive analytics, real-time tracking, and route optimization, FarEye empowers logistics professionals to achieve on-time deliveries, maintain product quality, control costs, optimize inventory, enhance delivery efficiency, and ensure safety and compliance—all while reducing their environmental impact. In today's competitive logistics landscape, FarEye is the game-changer that enables logistics managers to stay ahead of the curve and drive supply chain excellence.
Conclusion
Incorporating these logistics KPIs into your operations and continuously monitoring them empowers logistics managers to make data-driven decisions, enhance efficiency, and improve the overall performance of the supply chain. Remember that while these KPIs provide valuable insights, their successful implementation and impact ultimately depend on the dedication and expertise of your logistics team.
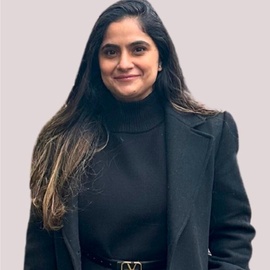
Komal Puri is a seasoned professional in the logistics and supply chain industry. As the AVP of Marketing and a subject matter expert at FarEye, she has been instrumental in shaping the industry narrative for the past decade. Her expertise and insights have earned her numerous awards and recognition. Komal’s writings reflect her deep understanding of the industry, offering valuable insights and thought leadership.
Let's Talk to Our Experts and Optimize Your Deliveries Today!
An expert from our team will reach out within 24 hours